Posadzki przemysłowe - warunki bezawaryjnej eksploatacji
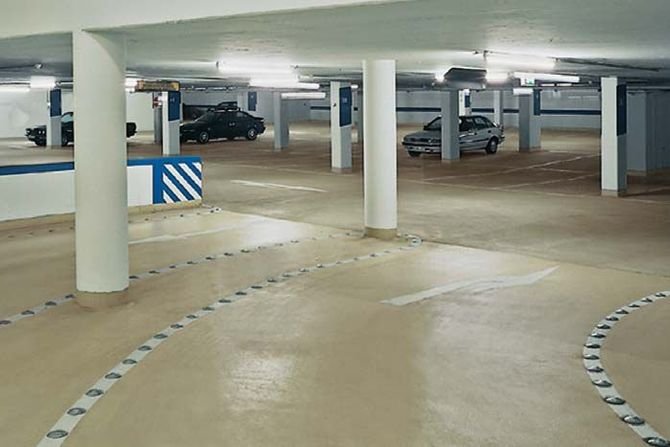
Fot. 1. Przykład polimerowo-cementowej posadzki przemysłowej
Deitermann
Pod pojęciem podłogi należy rozumieć wykończenie poziomej przegrody konstrukcji nadające jej wymagane właściwości użytkowe. Na podłogę składają się: warstwy hydroizolacyjne, paroizolacja, izolacje termiczne i akustyczne, warstwy ochronne, warstwy nośne (betony, jastrychy), dobrane w zależności od obciążeń, rodzaju pomieszczenia i związanych z tym wymagań użytkowych. Posadzka natomiast to wierzchnia warstwa podłogi, przenosząca na warstwy konstrukcji obciążenia użytkowe i/lub zabezpieczająca przed zniszczeniem na skutek agresywnych mediów.
Zobacz także
Tremco CPG Poland Sp. z o.o. Flowcrete – bezspoinowe posadzki żywiczne w przemyśle

Bezspoinowe posadzki żywiczne są często nazywane posadzkami przemysłowymi. Ze względu na ich właściwości, m.in. trwałość, wytrzymałość mechaniczną, w tym odporność na ścieranie, szczelność i nienasiąkliwość...
Bezspoinowe posadzki żywiczne są często nazywane posadzkami przemysłowymi. Ze względu na ich właściwości, m.in. trwałość, wytrzymałość mechaniczną, w tym odporność na ścieranie, szczelność i nienasiąkliwość oraz łatwość utrzymania w czystości, rozwiązania posadzkowe na bazie żywic syntetycznych są powszechnie stosowane w zakładach produkcyjnych z różnych branż.
dr inż. Krzysztof Pogan, WestWood® Kunststofftechnik GmbH Rozwiązania dla parkingów wielopoziomowych i podziemnych

Parkingi wielopoziomowe i podziemne to niewątpliwie budowle, których nie można porównać do powszechnie spotykanych w budownictwie tradycyjnych budowli żelbetowych. Swoimi właściwościami przypominają one...
Parkingi wielopoziomowe i podziemne to niewątpliwie budowle, których nie można porównać do powszechnie spotykanych w budownictwie tradycyjnych budowli żelbetowych. Swoimi właściwościami przypominają one raczej budowle drogowe, jak np. mosty. Zatem muszą spełniać wysokie wymagania w zakresie trwałości – powinny możliwie długo pozostać odporne na oddziaływanie warunków zewnętrznych i służyć przez długi czas.
mgr inż. Julia Blazy, prof. dr hab. inż. Łukasz Drobiec Wpływ zbrojenia rozproszonego na pracę posadzek na gruncie
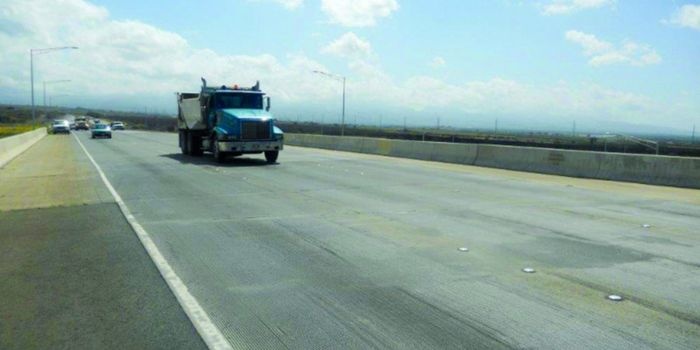
Temat zachowania się posadzek przemysłowych z dodatkiem zbrojenia rozproszonego (ang. fiber reinforced concrete – FRC) ma charakter interdyscyplinarny. Dlaczego? Otóż nie jest związany tylko z inżynierią...
Temat zachowania się posadzek przemysłowych z dodatkiem zbrojenia rozproszonego (ang. fiber reinforced concrete – FRC) ma charakter interdyscyplinarny. Dlaczego? Otóż nie jest związany tylko z inżynierią lądową i geotechniką, ale również z inżynierią materiałową. W rezultacie do poprawnego rozumienia pracy posadzki wymagana jest wszechstronna wiedza, której rozwój jest korzystny dla szerokiej grupy inżynierów oraz wykonawców. Ponadto ciągle jesteśmy świadkami rozwijających się nowych materiałów i...
Rozwiązania konstrukcyjne posadzek są różne w zależności od obciążeń i miejsca wbudowania (warunków eksploatacyjnych). Rodzaj zastosowanych materiałów zależy przede wszystkim od rodzaju pomieszczenia i obiektu, sposobu obciążenia, obecności i rodzaju agresywnych związków, sposobu użytkowania pomieszczenia, dodatkowych wymagań sanitarnych itp. (rys. 1).
Wybór rozwiązania materiałowego
Podstawowym warunkiem długotrwałej bezproblemowej eksploatacji posadzki jest przyjęcie poprawnego technicznie rozwiązania materiałowego związanego nie tylko z samą posadzką, lecz także z warstwami konstrukcji podłogi.
Chodzi tu nie tylko o zdolność do przenoszenia obciążeń użytkowych (mechanicznych - od nacisku kół, sił powstałych przy hamowaniu, dynamicznych, od uderzeń; termicznych, np. w chłodniach czy na parkingach otwartych; chemicznych itp.), lecz także o bezpieczeństwo użytkowania, zabezpieczenie wód gruntowych przed przedostaniem się do nich agresywnych substancji (jeżeli występują), odpowiednią izolacyjność termiczną oraz akustyczną, odporność na starzenie czy wreszcie łatwość w utrzymaniu czystości.
Biorąc pod uwagę, że podłoga musi współpracować z innymi elementami konstrukcji budynku (np. słupy, ściany), trzeba w niej nie tylko obsadzić, lecz także uszczelnić wpusty, odpowiednio skonstruować, a nierzadko i uszczelnić dylatacje konstrukcyjne, strefowe czy brzegowe. Konstruktor musi na etapie projektowania uwzględnić wszystkie czynniki mające wpływ na zachowanie się konstrukcji podłogi w trakcie eksploatacji. Do tego dochodzą zjawiska związane z ruchem wilgoci przez przegrodę, których zaniedbanie także może prowadzić do powstania uszkodzeń.
Poszczególne warstwy podłogi decydujące o trwałości konstrukcji
Dla konstrukcji ułożonych na gruncie pierwszą warstwą jest odpowiednio zagęszczone podłoże (piasek lub żwir) o grubości 20-30 cm. Następną warstwę stanowi beton podkładowy, układany na warstwie przerywającej podciąganie kapilarne.
Sam piasek nie przerywa podciągania kapilarnego - konieczne jest dodatkowe ułożenie przepony z membrany kubełkowej lub grubej folii PE zgrzewanej na zakładach. Podciąganie kapilarne może być przerwane przez warstwę płukanego żwiru o uziarnieniu 8-32 mm (a przynajmniej 8-16 mm) i grubości nie mniejszej niż 20 cm. Kolejną (licząc od spodu konstrukcji) jest warstwa izolacji przeciwwilgociowej, zapobiegająca penetracji wilgoci z gruntu w głąb konstrukcji. Wykonuje się ją z rolowych materiałów bitumicznych (pap termozgrzewalnych, membran samoprzylepnych), z powłok bezszwowych (bitumicznych mas modyfikowanych tworzywami sztucznymi - KMB) oraz ze zgrzewanych membran z tworzyw sztucznych. Przed zastosowaniem każdego z materiałów należy zwrócić uwagę na wilgotność i wysezonowanie podłoża.
Kolejnym elementem, który może mieć wpływ na trwałość rozwiązania konstrukcyjnego, jest warstwa termoizolacyjna. Szczególnie niebezpieczne jest stosowanie jako termoizolacji złej jakości materiału, nieodpornego na długotrwały nacisk i o niewielkiej wytrzymałości mechanicznej. Termoizolacja powinna przede wszystkim charakteryzować się odpowiednią ściśliwością, tj. odkształcalnością przy długotrwałym obciążeniu. Z tych względów zalecane jest stosowanie termoizolacji z polistyrenu ekstrudowanego (XPS) zgodnego z normą PN-EN 13164:2003. Wyroby z polistyrenu ekspandowanego (styropianu) zgodne z normą PN-EN 13163:2004 mogą być stosowane przy mniejszych obciążeniach mechanicznych. Co do klasy wiążące są wymagania normy PN-B-20132:2005 (np. EPS 200-036 dach/podłoga/parking, EPS 250-036 podłoga/parking).
Na warstwie termoizolacji wymagane jest ułożenie warstwy rozdzielającej. Jej podstawową funkcją jest zabezpieczenie płyt termoizolacyjnych przy wykonywaniu betonu nośnego. W przypadku obciążenia tylko wodą, bez obecności agresywnych czynników (lub przy ich bardzo niewielkim stężaniu), można zastosować zwykłą folię PE (o grubości przynajmniej 0,3-0,4 mm), układaną na zakład 20-30 cm. W pozostałych przypadkach stosuje się chemoodporne, sklejane lub zgrzewane na zakładach membrany. Są one bezwzględnie wymagane w przypadku obecności agresywnych mediów, działających destrukcyjnie na styropian (rozpuszczalniki: aceton, eter, octan etylu, nitro, benzen, ksylol, trojchloroetylen, czterochlorometan, terpentyna; węglowodory alifatyczne nasycone - cykloheksan, benzyna lakowa; paliwa silnikowe).
Do wykonywania warstwy rozdzielającej w takim przypadku stosuje się np:
- folie z polichlorku winylu (PVC) - są odporne na oddziaływanie kwasów organicznych, nieorganicznych i ługów (stężenia rzędu 10-20%) roztworów soli, a także olejów i tłuszczów. Nie są odporne na oddziaływanie np. rozpuszczalników organicznych, takich jak benzen i ksylen,
- folie poliizobutylenowe - stosuje się je przy oddziaływaniu kwasów organicznych i nieorganicznych o stężeniach nieprzekraczających 20%, roztworów ługów o stężeniach nieprzekraczających 30% oraz roztworów substancji utleniających i alkoholi (przy stężeniach do 5-10%),
- folie polietylenowe z polietylenu o wysokiej gęstości (HDPE) - cechują się odpornością chemiczną na oddziaływanie kwasów nieorganicznych o stężeniach do ok. 20%, kwasów organicznych o stężeniach do 10%, 20-25-proc. roztworów ługów oraz roztworów substancji utleniających (stężenie 20-25%).
Przy posadzkach przemysłowych na stropie układ warstw będzie zmodyfikowany. Będzie on zależał od charakteru obciążeń, wymagań cieplnych itp. Nie zawsze musi być wykonywana także warstwa termoizolacji.
Warstwa betonu nośnego musi umożliwić przejęcie przede wszystkim obciążeń mechanicznych oddziałujących na podłogę. Można zaryzykować, że jest to najprostszy wariant wykonania posadzki, jednakże płyta betonowa, nawet z betonów o wysokich parametrach wytrzymałościowych, nie jest w stanie spełnić wszystkich stawianych jej wymagań, chociażby ze względu na relatywnie wysoką ścieralność, nasiąkliwość, porowatość, niewielką odporność chemiczną itp.
Rodzaje posadzek
Wiele jest rozwiązań materiałowo-konstrukcyjnych samych posadzek, jednak najczęściej wykonuje się posadzki betonowe oraz żywiczne. W przypadku posadzek betonowych konieczne jest wykonanie dodatkowych zabiegów polegających na:
- wykonaniu posypki utwardzającej ze specjalnych preparatów zwierających spoiwo (cement) oraz kruszywo korundowe, kwarcowe, bazaltowe itp.
- utwardzeniu powierzchni mieszankami zapraw,
- impregnacji powierzchniowej (utwardzeniu) preparatami krzemianowymi,
- impregnacji polimerami,
- wykonaniu warstwy wierzchniej z zaprawy polimerowo-cementowej (wylewanej lub zacieranej).
Posadzki żywiczne wykonuje się najczęściej z syntetycznych żywic:
- epoksydowych,
- poliuretanowych,
- akrylowych,
- na bazie polimetakrylanu metylu.
Wykonywane były także posadzki na bazie żywic winylowo-estrowych. Można także wyróżnić posadzki bitumiczne, z płytek ceramicznych, anhydrytowe, magnezjowe. Ostateczny dobór warstw konstrukcji podłogi musi:
- zapewnić odpowiednią odporność na obciążenia użytkowe: mechaniczne, termiczne, chemiczne itp.,
- zabezpieczyć przed przedostawaniem się agresywnych substancji do wód gruntowych,
- zapewnić odpowiednie bezpieczeństwo użytkowania.
Takie zróżnicowanie technologii wynika z różnych wymagań stawianych posadzkom przemysłowym: inne będą w odniesieniu do posadzek w magazynach czy halach wysokiego składowania, inne - w magazynach towarów suchych, odmienne - w halach z produkcją mokrą, a jeszcze inne na parkingach otwartych, krytych itp. Sama płyta betonowa jest wrażliwa na agresywne media, trudna w utrzymaniu czystości, o ograniczonej odporności na ścieranie, w mniejszym lub większym stopniu nasiąkliwa. Nie może ona też spełniać wymogów antypoślizgowości (jeżeli są one w tym wypadku niezbędne).
Nadawanie powierzchni posadzki odpowiednich parametrów wytrzymałościowych
Z punktu widzenia trwałości posadzki bardzo istotne jest zastosowanie betonu o odpowiednich parametrach wytrzymałościowych. Należy pamiętać, że największe obciążenia mechaniczne są powodowane przez małe koła metalowe lub z tworzyw sztucznych (rys. 2). Dlatego obciążenia mechaniczne, np. w piekarni, gdzie odbywa się ruch wozków, mogą być większe niż w magazynie, gdzie odbywa się ruch nawet mocno obciążonych wozków na kołach pompowalnych lub z twardej gumy (tabela 1).
Tanią, lecz skuteczną metodą nadawania powierzchni posadzki odpowiednich parametrów wytrzymałościowych jest powierzchniowe utwardzanie specjalnymi suchymi posypkami wcieranymi w warstwę świeżego betonu. Postęp w dziedzinie technologii betonu oraz modyfikacje składu posypek utwardzających spowodowały, że sposób ten jest coraz chętniej stosowany, zwłaszcza tam, gdzie nie występują oddziaływania chemiczne, a głównym wymogiem jest wysoka wytrzymałość mechaniczna i odporność na ścieranie.
W skład posypek wchodzą zasadniczo: wyselekcjonowane cementy i kruszywo, żywice ułatwiające zacieranie i powodujące, że posypka po stwardnieniu tworzy monolit z podłożem. Jako składniki zwiększające odporność na ścieranie i obciążenia dynamiczne stosuje się zazwyczaj drobnoziarniste kruszywa korundowe i elektrokorundowe (choć spotykane są też posypki na bazie kwarcu). Wykonanie takiej warstwy utwardzającej wymaga dwukrotnego posypania powierzchni świeżego betonu odpowiednią ilością suchej posypki i wtarcie jej w beton za pomocą mechanicznych zacieraczek (najpierw talerzowych, a po upływie kilkudziesięciu minut - łopatkowych).
Do pielęgnacji tak wykonanej posadzki po utwardzeniu stosuje się specjalne impregnaty zawierające najczęściej żywice akrylowe albo epoksydowe. Takie posypki mogą ponadto zwiększać odporność na szkodliwe czynniki atmosferyczne oraz wnikanie olejów i tłuszczów, nie stanowią jednak szczelnej powłoki, są wrażliwe na zarysowania podłoża oraz dają gładką powierzchnię. Nie zwiększają także w zasadniczy sposób odporności chemicznej posadzki.
Wadą posypek utwardzających jest możliwość ich stosowania tylko na niezwiązanym do końca betonie. Nie da się ich zastosować na posadzkach naprawianych. Rozwiązaniem są wówczas specjalne, polimerowo-cementowe zaprawy, pozwalające na uzyskanie bardzo wytrzymałej i trwałej nawierzchni, odpornej na ścieranie, uderzenia, działanie wody, alkaliów, oddziaływania kół pojazdów oraz inne obciążenia przemysłowe. Zaprawy tego typu mogą występować w postaci samopoziomującej i/lub szybkowiążącej (ruch pieszy jest możliwy już po 2-5 godz., lekkie obciążenie po 24 godz., a pełne obciążenie po 7 dniach). Ich zaletą jest to, że nie wymagają zacierania ani specjalnych zabiegów pielęgnacyjnych. Grubość warstwy zaprawy zależy od przewidywanych obciążeń. Przy obciążeniach ruchem pojazdów o nacisku na oś powyżej 3,5 t na kołach gumowych pompowalnych oraz ruchem pojazdów o nacisku na oś powyżej 600 kg na kołach z tworzyw twardych może być konieczne ułożenie dwóch warstw. Możliwe jest także dodatkowe zabezpieczenie takiej posadzki lakierem żywicznym. Schemat takiej posadzki dwuwarstwowej pokazano na rys. 3, natomiast gotową posadzkę na fot. 1.
Powierzchniowym zabezpieczeniem posadzki jest również jej impregnacja. Do tego celu stosuje się zazwyczaj epoksydowe impregnaty na bazie rozpuszczalników (w porównaniu z preparatami dyspersyjnymi cechują się one większą zdolnością do penetracji w podłoże), choć spotyka się już także preparaty bezrozpuszczalnikowe. Efektem jest zwiększenie wytrzymałości na ściskanie i zginanie, zmniejszenie nasiąkliwości, zwiększenie odporności chemicznej oraz poprawa estetyki posadzki. Impregnaty nie tworzą jednak ciągłej, szczelnej powłoki. Mogą być (i często są) stosowane na posypkach utwardzających oraz posadzkach polimerowo- cementowych. Mogą wówczas pełnić rolę ochronną (zapobiegającą zbyt szybkiemu wysychaniu) oraz rolę typowego impregnatu.
Rozwiązania posadzek o zwiększonych wymaganiach wytrzymałościowych
Opisane metody - posypka, zaprawy polimerowo-cementowe - w wielu wypadkach nie mogą być stosowane, jeśli powierzchnia ma być obciążona termicznie, chemicznie i mechanicznie, należy jej zapewnić znacznie większą odporność na ścieranie, odporność chemiczną, szczelność oraz bezpieczeństwo użytkowania (odpowiednią antypoślizgowość, także w warunkach zalegania płynówna powierzchni). W tym celu należy stosować posadzki z żywic syntetycznych lubz płytek ceramicznych.
Rodzaje i zalety żywic
Cechą żywic epoksydowych jest wysoka odporność mechaniczna (wytrzymałość na ściskanie rzędu 40-90 N/mm2, wytrzymałość na zginanie rzędu 20-40 N/mm2, wytrzymałość na rozciąganie rzędu 12-20 N/mm2), twardość i odporność na ścieranie, uderzenia czy zarysowania. Z tym wiąże się jednak sztywność powłoki. Epoksydy są mniej wrażliwe na wilgotność resztkową podłoża i wysoką wilgotność powietrza podczas aplikacji i twardnienia niż żywice poliuretanowe.
Zaletą żywic epoksydowych jest odporność na agresywne media, zarówno kwaśne, jak i alkaliczne. Są odporne na roztwory kwasów nieorganicznych i organicznych (z wyjątkiem fluorowodorowego i octowego), roztwory soli nieorganicznych i wodorotlenków oraz na materiały pędne i smary. Ograniczoną odporność wykazują na substancje utleniające (chlor, kwas azotowy), alkohole (np. metanol), estry (np. octany butylu), ketony czy węglowodory. Poza tym epoksydy są odporne na wpływy atmosferyczne. Jedynym ich mankamentem jest skłonność do żółknięcia i kredowania pod wpływem promieniowania UV. Nie wpływa to jednak negatywnie na parametry użytkowe powłoki.
Dwuskładnikowe żywice poliuretanowe w przeciwieństwie do epoksydowych są elastyczne, mają zdolność mostkowania rys podłoża oraz są bardziej odporne na uderzenia, i to w niskich temperaturach. Są także odporne na promieniowanie UV oraz na starzenie. Ich parametry wytrzymałościowe są jednak niższe niż epoksydów, zwłaszcza dotyczy to odporności na ścieranie (wytrzymałość na rozciąganie rzędu 2,2-3,5 N/mm2, wydłużenie względne przy rozciąganiu do 160%). Są odporne na paliwa (materiały pędne), smary, rozcieńczone kwasy i zasady, a także na oleje, tłuszcze, aromatyczne węglowodory i estry. Są mniej odporne na stężone zasady, zwłaszcza w podwyższonych temperaturach, oraz na ketony.
Jednoskładnikowe żywice poliuretanowe są ogólnie rzecz biorąc odporne na paliwa (materiały pędne), smary, rozcieńczone kwasy i zasady. Są niewrażliwe na wpływy atmosferyczne.
Właściwością przypisaną wszystkim poliuretanom jest ich wrażliwość na wilgoć w podłożu i wysoką wilgotność względną powietrza. Dotyczy to zarówno momentu aplikacji, jak i procesu sieciowania. Wymaga to szczególnej ochrony (do momentu stwardnienia) przed oddziaływaniem wilgoci.
Spotyka się także żywice będące swoistymi hybrydami, np. epoksydowo-poliuretanowe. Wykazują one cechy właściwe zarówno epoksydom, jak i poliuretanom, np. elastyczność w połączeniu z odpornością na ścieranie.
Żywice z polimetakrylanu metylu z kolei cechują się szybkim czasem utwardzania (nawet dochodzącym do 60 min) oraz możliwością układania w niskich (ujemnych) temperaturach. Z parametrów wytrzymałościowych należy wymienić dobrą trwałość, odporność na uderzenia oraz dobrą wytrzymałość mechaniczną.
Zastosowanie żywic w posadzkach typu powłokowego,wylewanego, szpachlowego
Kompozycje żywic syntetycznych służą do wykonywania posadzek typu:
- powłokowego - grubość kompozycji żywicznej maks. 0,5-1 mm - będą to warstwy lakiernicze oraz posadzki wylewane cienkowarstwowe,
- wylewanego - grubość kompozycji żywicznej wynosi 1,5-4 mm - są to posadzki grubowarstwowe,
- szpachlowego - grubość kompozycji żywicznej rzędu 3-25 mm; ze względu na cenę stosowane są najrzadziej - tylko przy bardzo ciężkich warunkach eksploatacyjnych i przy oddziaływaniu bardzo agresywnego środowiska.
Najprostszym sposobem zabezpieczenia powierzchni jest wykonanie powłoki ochronnej (lakierowania) - rys. 4. Wykonuje się ją jako np. dwu-, trzykrotne naniesienie żywicy. Nie jest wymagany osobny gruntownik - jego rolę pełni warstwa nakładana w pierwszym przejściu. Taka powłoka wykonywana jest jako gładka. Drugim wariantem tego rozwiązania jest naniesienie żywicy gruntującej, na którą nakłada się żywicę będącą właściwą powłoką ochronną (parametry żywicy gruntującej związane są z innymi wymaganiami) - rys. 5. To rozwiązanie pozwala na uzyskanie powłoki antypoślizgowej rys. 6.
Posadzki cienkowarstwowe (rys. 7 i 8) stosuje się w pomieszczeniach nienarażonych na intensywne obciążenia ruchem kołowym i przy słabym lub ograniczonym oddziaływaniu agresywnych mediów (przy takich obciążeniach mogą być także stosowane powłoki lakiernicze). W praktyce są to obiekty budownictwa ogólnego (lub użyteczności publicznej). W ograniczonym stopniu tego typu posadzki wykonuje się w budownictwie przemysłowym.
Posadzki grubowarstwowe (rys. 9 i 10) epoksydowe stosuje się w budownictwie przemysłowym, użyteczności publicznej i budownictwa ogólnego przy wysokich obciążeniach mechanicznych i obecności agresywnych mediów. Żywice poliuretanowe w tego typu posadzkach stosuje się tam, gdzie jest konieczność zastosowania materiału elastycznego. Należy jednak pamiętać, ze odporność poliuretanów na oddziaływanie agresywnych substancji chemicznych jest mniejsza niż odporność epoksydów.
Z drugiej strony żywice epoksydowe są w znacznie mniejszym stopniu odporne na UV, nie tracą wprawdzie swych właściwości, jednak w wielu sytuacjach ważny jest także aspekt estetyczny. Spotyka się także żywice poliuretanowo-epoksydowe cechujące się większą odpornością mechaniczną i chemiczną niż posadzka poliuretanowa przy pewnej elastyczności, czego z kolei pozbawiona jest posadzka epoksydowa.
Systemy posadzek cienko- lub grubowarstwowych składają się z:
- gruntownika,
- warstwy pośredniej,
- warstwy zamykającej (lakierowania), przy czym wykonanie warstwy zamykającej może być opcjonalne, zatem warstwa pośrednia jest warstwą użytkową. Możliwa jest jednak sytuacja, że warstwy użytkowe są bardziej rozbudowane.
Na świeżej warstwie żywicy gruntującej wykonuje się posypkę ze specjalnego piasku kwarcowego przeznaczonego do stosowania z żywicami. Jego uziarnienie zazwyczaj wynosi 0,2-0,7 mm, a po związaniu gruntownika nadmiar piasku się usuwa. Na tak przygotowaną warstwę gruntującą nakłada się warstwę o określonej grubości materiału będącego właściwą powłoką ochronną. Jeżeli nie jest wymagana antypoślizgowość czy nadanie specyficznego wyglądu (matowego, z połyskiem), wykonanie posadzki można uznać za zakończone (rys. 7 i 9). W przeciwnym wypadku konieczne jest polakierowanie specjalnymi żywicami (zazwyczaj poliuretanowymi jednoskładnikowymi lakierami). Przy wersji antypoślizgowej (rys. 8 i 10) świeżo nałożoną żywicę trzeba posypać piaskiem kwarcowym lub korundem o określonym uziarnieniu, zależnym od wymaganej klasy antypoślizgowości i przestrzeni wypełnienia (tabela 2), i po usunięciu niezwiązanego piasku wykonać lakierowanie zamykające.
Epoksydowe żywice do wykonywania powłok grubowarstwowych mogą być mieszane z piaskiem do żywic (takim samym jak do wykonywania posypki). Zwiększa to odporność związanej żywicy na obciążenia mechaniczne (oraz zmniejsza przy okazji koszt materiału), może jednak wpływać negatywnie na odporność chemiczną. Proporcje mieszania podaje zawsze producent systemu (wagowo mogą się one wahać od 0,5 do nawet 2 części piasku na 1 część żywicy). Im większa ilość dodawanego piasku, tym gorsza rozlewność masy. Ograniczeniem jest konieczność wykonania warstwy o podanej przez producenta minimalnej grubości.
Żywice poliuretanowe często stosuje się jako posadzki na parkingach narażonych na oddziaływanie czynników, jako wykończenie powierzchni balkonów oraz wszędzie tam, gdzie konieczne jest zastosowanie elastycznej, mostkującej rysy powłoki.
Do żywic poliuretanowych piasku z reguły się nie dodaje. Co prawda, niektórzy producenci w kartach technicznych dopuszczają taką możliwość, jednakże należy do tego podchodzić bardzo ostrożnie. Dodatek piasku do żywic poliuretanowych znacznie pogarsza ich elastyczność. Dlatego jego ilość nie przekracza zazwyczaj 0,4-0,5 części wagowych. Uwaga: powłoka z żywicy poliuretanowej zachowuje elastyczność, gdy jej grubość wynosi przynajmniej 1,5 mm.
Zastosowanie żywic na powierzchniach parkingów
Zróżnicowanie systemów posadzek z żywic łatwo przedstawić na przykładzie nawierzchni parkingów. Spotyka się rozwiązania z zastosowaniem żywic poliuretanowych, poliuretanowo-epoksydowych oraz epoksydowych. Wybór materiału zależy od miejsca jego wbudowania (umiejscowienia posadzki – na parkingu na dachu, w ogrzewanej hali, na stropach pośrednich itp.)
Najbardziej narażone na oddziaływania mechaniczne oraz warunki atmosferyczne są parkingi na dachach. Oprócz obciążeń dynamicznych podlegają znacznym obciążeniom termicznym (gradient temperaturowy lato–zima dochodzi do 100ºC), oddziaływaniu promieniowania UV, środków odladzających oraz paliwa, olejów i płynów eksploatacyjnych. Z tych względów zastosowany materiał musi cechować się przede wszystkim elastycznością i odpornością na UV. Najlepiej do tych celów stosować żywice poliuretanowe.
Grubość warstw użytkowych wynosi zazwyczaj 3-5 mm. Najczęściej spotyka się dwa warianty takiej posadzki:
- na gruntowniku układana jest warstwa elastycznej żywicy poliuretanowej o grubości 1,5-2 mm, a na niej druga warstwa (3-4 mm) także elastycznego poliuretanu, lecz o większej odporności na ścieranie,
- na gruntowniku układa się warstwę elastycznej, lecz odpornej na ścieranie żywicy poliuretanowej (ewentualnie poliuretanowo-epoksydowej) o grubości 2-4 mm. W obu wypadkach powierzchnia posadzki musi być szorstka, dlatego świeżą warstwę żywicy należy posypać kruszywem (piaskiem kwarcowym, korundem) o odpowiednim uziarnieniu (tabele 2 i 3) i polakierować odpornym na UV lakierem poliuretanowym.
W przypadku parkingów podziemnych lub parkingów zakrytych, gdzie nie ma obciążenia zmianami temperatury, zamiast żywicy poliuretanowej stosuje się żywicę epoksydową, często z dodatkiem piasku kwarcowego, co zwiększa jej odporność mechaniczną. Warstwa zamykająca (tu można stosować zarówno żywice epoksydowe, jak i poliuretanowe) wykonywana jest także na posypce nadającej antypoślizgowość. Konstrukcja ta nie ma możliwości mostkowania rys.
Płyty stropów pośrednich w parkingach otwartych także są narażone na oddziaływania termiczne, jednakże nie aż tak duże. Dlatego oprócz żywic poliuretanowych można tu stosować także elastyczne żywice poliuretanowo-epoksydowe. Grubość warstwy nośnej wynosi zazwyczaj 3-4 mm. Konieczne jest również wykonanie lakierowania zamykającego nadającego antypoślizgowość.
Podane grubości warstw są grubościami przeciętnymi, w zależności od obciążeń (samochody ciężarowe, osobowe) mogą one być zwiększone lub zmniejszone, jednak nie bezkrytycznie. Żywice poliuretanowe cechują się zdolnością mostkowania rys, gdy są ułożone w warstwie min. 1,5-2 mm.
Zawsze trzeba zwrócić uwagę na dyfuzję pary wodnej w przegrodzie i odpowiednio zapobiegać negatywnym skutkom: np. przez wykonanie odpowiednich warstw paroszczelnych, wymalowania o dużym oporze dyfuzyjnym, specjalnych gruntowników epoksydowych będących warstwą paroszczelną, stosowanie żywic cechujących się pewną zdolnością do dyfuzji pary wodnej.
Uwarunkowania dotyczące bezpieczeństwa
Posadzka powinna być bezpieczna w użytkowaniu. Problem ten dotyczy przede wszystkim posadzek o mokrej powierzchni, powierzchni narażonych na oddziaływania atmosferyczne oraz powierzchni pochyłych (np. podjazdów, ramp). O bezpieczeństwie użytkowania decydują dwa parametry:
- antypoślizgowość, definiowana strukturą wierzchniej warstwy, przy której przy nachyleniu pod odpowiednim kątem noga w typowym obuwiu roboczym nie poślizgnie się. Klasy antypoślizgowości oznacza się symbolami od R 9 do R 13 (tabela 3),
- przestrzeń wypełnienia - zdolność do gromadzenia zanieczyszczeń, zarówno ciekłych, jak i stałych, w sposób niepowodujący niebezpieczeństwa poślizgu. Jest to realizowane poprzez uzyskanie wolnej przestrzeni pomiędzy najniższym a najwyższym punktem warstwy użytkowej posadzki (rys. 11). Rozróżnia się cztery klasy przestrzeni wypełnienia: V 4, V 6, V 8 i V 10 (cyfra mówi o objętości dostępnej przestrzeni w 1 cm³ na 1 dm³ powierzchni posadzki).
Wymaganą antypoślizgowość posadzek bezspoinowych z żywic epoksydowych i/lub poliuretanowych nadaje się, wykonując na świeżo ułożonej warstwie żywicy posypkę z piasku kwarcowego lub korundu. Po związaniu nadmiar piasku należy usunąć i polakierować powierzchnę (fot. 2, tabela 2).
Zdolnością odprowadzania ładunków cechują się posadzki antyelektrostatyczne. Taki system występuje w wariancie gładkim:
- gruntownik systemowy,
- taśma i lakier przewodzący,
- warstwa użytkowa (przewodząca) - grubowarstwowa żywica epoksydowa
lub poliuretanowa lub szorstkim (antypoślizgowym) z przewodzącą posypką:
- taśma przewodząca,
- systemowy gruntownik,
- posypka przewodząca,
- warstwa użytkowa (przewodząca) - cienkowarstwowa żywica epoksydowa
lub poliuretanowa albo przewodzącym lakierem:
- systemowy gruntownik,
- taśma i lakier przewodzący,
- posypka przewodząca,
- warstwa użytkowa (przewodząca) - cienkowarstwowa żywica epoksydowa lub poliuretanowa.
Zastosowanie żywic na ścieżkach rowerowych
Pewną odmianą posadzek przemysłowych, o której warto wspomnieć, są ścieżki rowerowe. Nawet jeżeli ich podłożem jest asfalt, zastosowanie odpowiednich żywic pozwala uzyskać ciekawy wizualnie efekt (fot. 3) oraz, co ważniejsze, bardzo dobrą antypoślizgowość powierzchni (fot. 4). Coraz więcej rowerzystów spotyka się także zimą, a odśnieżanie chodników i dróg pozostawia wiele do życzenia.
Podstawowym problemem, który musiał tu zostać rozwiązany, jest zapewnienie dobrej przyczepności warstw systemu do podłoża asfaltowego, elastyczności i odporności na czynniki atmosferyczne oraz odpowiedniej antypoślizgowości. Warstwą użytkową jest tu specjalna dwuskładnikowa żywica poliuretanowa o niewielkiej zawartości rozpuszczalnika. Jej skład chemiczny został tak dobrany, by powłoka mogła być wykonywana na podłożach mało stabilnych takich jak podłoża asfaltowe. Nie jest tu wymagany osobny gruntownik. Po nałożeniu żywicy wykonuje się na niej posypkę ze specjalnego piasku kwarcowego o uziarnieniu 0,7-1,2 mm oraz warstwę zamykającą z dwuskładnikowej poliuretanowej barwionej żywicy cechującej się bardzo dobrą zdolnością krycia, odpornością na działanie słońca i promieni UV, a także na oddziaływanie ropopochodnych paliw, smarów, środków odladzających itp. Musi ona dodatkowo cechować się odpornością na obciążenia mechaniczne i ścieranie.
Posadzka z płytek ceramicznych
Posadzka przemysłowa może być wykonana także z płytek ceramicznych. W przypadku obciążenia wodą i/lub agresywnymi mediami oraz w pomieszczeniach mokrych konieczne jest wykonanie uszczelnienia zespolonego. Do tego celu służą specjalne chemoodporne reaktywne żywice poliuretanowe lub epoksydowe, tworzące elastyczne uszczelnienie podpłytkowe.
Rozwiązanie z uszczelnieniem zespolonym i okładziną ceramiczną wymaga nie tylko zaprojektowania ułożenia płytek, lecz także określenia w dokumentacji technicznej albo konkretnego rodzaju płytek, albo minimalnych parametrów, którymi muszą się one cechować. To bardzo istotne, ponieważ płytki te muszą spełniać wymogi dotyczące odporności mechanicznej, odporności na zabrudzenia czy bezpieczeństwa użytkowania (śliskości). Klasę antypoślizgowości i/lub przestrzeni wypełnienia dla płytek deklaruje producent. Przykłady płytek z zadeklarowaną klasą antypoślizgowości i/lub przestrzeni wypełnienia pokazano na fot. 5-6. Należy stosować płytki odporne na ścieranie, o twardej i nienasiąkliwej strukturze, odporne na plamienie i agresję chemiczną oraz o odpowiednich parametrach wytrzymałościowych (płytki ciągnione klasy A I, ewentualnie A IIa oraz prasowane, klasyfikowane jako B Ia, B Ib oraz B IIa według normy PN-EN 14411:2005 .
Im większa grubość płytek, tym wyższe ich parametry wytrzymałościowe. W praktyce minimalna grubość płytek, pozwalająca na zgodną z przeznaczeniem eksploatację posadzki przemysłowej, to 12 mm, natomiast stosuje się także płytki znacznie grubsze (w przypadku dużych obciążeń mechanicznych stosuje się chemoodporne płytki o grubościach 16-40 mm, przy obciążeniach ruchem pieszym oraz małymi wózkami widłowymi na ogumionych kołach wystarczają płytki o grubości 12-16 mm). Wymogi higieniczne (częste czyszczenie) wymuszają zastosowanie płytek odpornych na ścieranie, o twardej i nienasiąkliwej strukturze oraz odpornych na plamienie. Niska nasiąkliwość to wymóg przy obciążeniach olejem i smarami.
Wymogi stawiane płytkom ceramicznym można usystematyzować w następujący sposób:
- odporność na uderzenie według PN-EN ISO 10545-5:1999 - istotna w przypadku płytek stosowanych w miejscach, gdzie odporność na uderzenie jest szczególnie ważna. W przypadku normalnych wymagań współczynnik odbicia wynosi 0,55,
- liniowa rozszerzalność cieplna według PN-EN ISO 10545-8:1998 - badanie to jest istotne dla płytek i płyt ceramicznych, które są stosowane w warunkach dużych różnic temperatur,
- odporność na szok termiczny według PN-EN ISO 10545-9:1998 - badanie powinno być stosowane w odniesieniu do płytek i płyt ceramicznych, które mogą być poddane miejscowej nagłej zmianie temperatury,
- mrozoodporność według PN-EN ISO 10545-12:1999 - istotna tylko w odniesieniu do wyrobów, które mają zastosowanie tam, gdzie występują ujemne temperatury,
- odporność chemiczna według PN-EN ISO 10545-13:1999 dotyczy płytek i płyt ceramicznych, jeśli istnieje możliwość, że będą narażone na niszczące działanie odczynników chemicznych,
- odporność na plamienie według PN-EN ISO 10545-14:1999 - badanie obowiązkowe w odniesieniu do płytek i płyt ceramicznych szkliwionych. W wypadku płytek i płyt nieszkliwionych, które mogą być narażone na plamienie, zalecana jest konsultacja z producentem,
- oznaczanie uwalnianego kadmu i ołowiu z płytek szkliwionych według PN-EN ISO 10545-15:1999 - badanie to jest wykonywane w przypadku płytek i płyt szkliwionych stosowanych na powierzchniach ścian i blatach, gdzie przygotowuje się żywność i gdzie produkty żywnościowe mogą mieć bezpośredni kontakt z powierzchnią szkliwioną,
- parametry wytrzymałościowe - największe obciążenia mechaniczne powodują małe koła metalowe lub z tworzyw sztucznych (rys. 2), dlatego wymagana odporność mechaniczna płytek ułożonych w piekarni może być większa niż w magazynie, gdzie odbywa się ruch wózków (dotyczy to także doboru grubości posadzki żywicznej). Miarą wytrzymałości mechanicznej jest wytrzymałość na zginanie i związana z nią siłą łamiąca: - siła łamiąca poniżej 1500 N - zastosowanie możliwe przy normalnym obciążeniu, tzn. w budownictwie mieszkaniowym, łazienkach itp.,
- - siła łamiąca 1500-3000 N - możliwe obciążenia ruchem kołowym - koła pompowane, drobny przemysł, administracja, handel,
- - siła łamiąca 3000-5000 N - możliwe obciążenia ruchem kołowym - koła gumowe pełne i pompowane - naprężenia do 6 MPa, przemysł.
- - siła łamiąca 5000-8000 N - możliwe obciążenia ruchem kołowym - koła z tworzyw sztucznych i stalowe - naprężenia 6–20 MPa, przemysł, supermarkety,
- - siła łamiąca powyżej 8000 N - możliwe obciążenia ruchem kołowym – koła stalowe – naprężenia powyżej 20 MPa.
- Wymóg wykonania posadzki antyelektrostatycznej nie wyklucza zastosowania płytek ceramicznych.
Dylatacje, odwodnienia
Równie ważnym elementem w całej konstrukcji, co poszczególne warstwy podłogi, są dylatacje, połączenia posadzki ze ścianą czy np. odwodnienia, zarówno liniowe, jak i punktowe. O jakości i trwałości posadzki w dużym stopniu decydują także: prawidłowe zaprojektowanie dylatacji, jej umiejscowienie, wyprofilowanie, sposób uszczelnienia oraz dobór materiału do wypełnienia (zazwyczaj stosuje się masy poliuretanowe, poliuretanowo- epoksydowe i tiokolowe) - odpornego na projektowane obciążenia mechaniczne, chemiczne i termiczne. Przy projektowaniu i wykonywaniu wpustów należy zwrócić uwagę nie tylko na spadki, lecz także, co istotne w przypadku dużych obciążeń mechanicznych, na sposób obsadzenia (np. na zaprawę czy klej epoksydowy), uszczelnienia (kołnierze) oraz zabezpieczenia przed mechanicznym uszkodzeniem.
Literatura
- PN-EN 13164:2003 "Wyroby do izolacji cieplnej w budownictwie. Wyroby z polistyrenu ekstrudowanego (XPS) produkowane fabrycznie. Specyfikacja".
- PN-EN 13163:2004 "Wyroby do izolacji cieplnej w budownictwie. Wyroby ze styropianu (EPS) produkowane fabrycznie. Specyfikacja".
- PN-B-20132:2005 "Wyroby do izolacji cieplnej w budownictwie. Wyroby ze styropianu (EPS) produkowane fabrycznie. Zastosowania".
- L. Czarnecki, B. Chmielewska, "Uszkodzenia i naprawy posadzek przemysłowych", XXIII Ogólnopolska Konferencja WPPK, Szczyrk 2008.
- BEB, "Industrieboeden aus Reaktionsharz. Stoffe", 1987.
- BEB, "Industrieboeden aus Reaktionsharz. Impraegnierung", 1985.
- BEB, "Industrieboeden aus Reaktionsharz. Beschichtung", 1985.
- BEB, "Industrieboeden aus Reaktionsharz. Versiegelung", 1985.
- PN-EN 14411:2005 "Płytki i płyty ceramiczne. Definicje, klasyfikacja, charakterystyki i znakowanie".
- PN-EN ISO 10545-5:1999 "Płytki i płyty ceramiczne. Oznaczanie odporności na uderzenie metodą pomiaru współczynnika odbicia".
- PN-EN ISO 10545-8:1998 "Płytki i płyty ceramiczne. Oznaczanie cieplnej rozszerzalności liniowej".
- PN-EN ISO 10545-9:1998 "Płytki i płyty ceramiczne. Oznaczanie odporności na szok termiczny".
- PN-EN ISO 10545-12:1999 "Płytki i płyty ceramiczne. Oznaczanie mrozoodporności".
- PN-EN ISO 10545-13:1999 "Płytki i płyty ceramiczne. Oznaczanie odporności chemicznej".
- PN-EN ISO 10545-14:1999 "Płytki i płyty ceramiczne. Oznaczanie odporności na plamienie".
- PN-EN ISO 10545-15:1999 "Płytki i płyty ceramiczne. Oznaczanie uwalnianego ołowiu i kadmu z płytek szkliwionych".
- "Warunki techniczne wykonania i odbioru robot budowlanych", Część B: "Roboty wykończeniowe", Zeszyt 3: "Posadzki mineralne i żywiczne", ITB, 2006.
- "Specyfikacje techniczne wykonania i odbioru robot budowlanych. Posadzki z żywic epoksydowych i poliuretanowych", Promocja 2007.
- PN-EN ISO 11600:2004 "Konstrukcje budowlane. Wyroby do uszczelniania. Klasyfikacja i wymagania dotyczące kitów".
- M. Rokiel, "Hydroizolacje w budownictwie. Wybrane zagadnienia w praktyce", wyd. II, Dom Wydawniczy MEDIUM 2009.
- BGR 181, "Fussböden in Arbeitsraumen und Arbeitsbereichen mit Rutschgefahr. Hauptverband der gewerblichen Berufsgenossenschaften", X 2003.
- PN-EN 206-1: 2003 "Beton. Część 1: Wymagania, właściwości, produkcja i zgodność".
- Materiały firm: Agrob Buchtal, Deitermann, Maxit, Schomburg.
IZOLACJE 9/2009