Wtórna hydroizolacja budynków – materiały bentonitowe
Materials used for the secondary waterproofing of buildings – bentonite materials
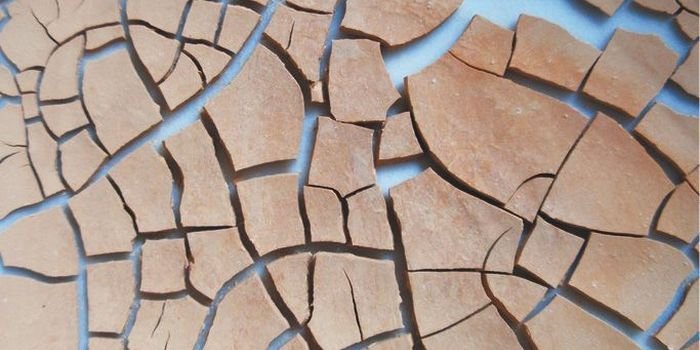
FOT. 1. Wysuszony bentonit; fot.: Wikimedia Commons
W przeszłości w budownictwie powszechnie wykorzystywano specyficzne właściwości gliny, która wprawdzie chłonie wodę, lecz jednocześnie zatrzymuje ją, nie przepuszczając dalej [1]. Materiał ten przez stulecia z powodzeniem stosowano do uszczelniania budynków – nawet jeśli wymagania stawiane „suchej” piwnicy nie były tak wysokie jak dzisiaj, glina pozwalała znacznie poprawić sytuację zawilgocenia. Z czasem lokalnie dostępną glinę zaczęto częściowo modyfikować przez stosowanie dodatków, m.in. mułów, wody i piasku. Współcześnie glina nie jest już wykorzystywana do hydroizolacji budynków – w tym celu wykorzystywany jest inny minerał ilasty: bentonit [2]. Z uwagi na długą tradycję stosowania, naturalne pochodzenie, odwracalność właściwości, jak również dobrą przepuszczalność pary wodnej, rozwiązania wykorzystujące bentonit są popularne w niektórych środowiskach konserwatorskich i stosowane są jako zabezpieczenie przed wilgocią kościołów i innych obiektów zabytkowych [3].
Zobacz także
Bostik Bostik AQUASTOPP – szybkie i efektywne rozwiązanie problemu wilgoci napierającej
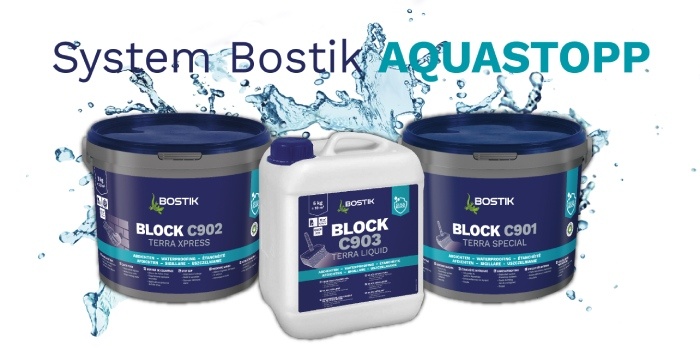
Bostik to firma z wieloletnią tradycją, sięgającą 1889 roku, oferująca szeroką gamę produktów chemii budowlanej dla profesjonalistów i majsterkowiczów. Producent słynie z innowacyjnych rozwiązań i wysokiej...
Bostik to firma z wieloletnią tradycją, sięgającą 1889 roku, oferująca szeroką gamę produktów chemii budowlanej dla profesjonalistów i majsterkowiczów. Producent słynie z innowacyjnych rozwiązań i wysokiej jakości preparatów, które znajdują zastosowanie w budownictwie, przemyśle i renowacji.
RAXY Sp. z o.o. Nowoczesne technologie w ciepłych i zdrowych budynkach
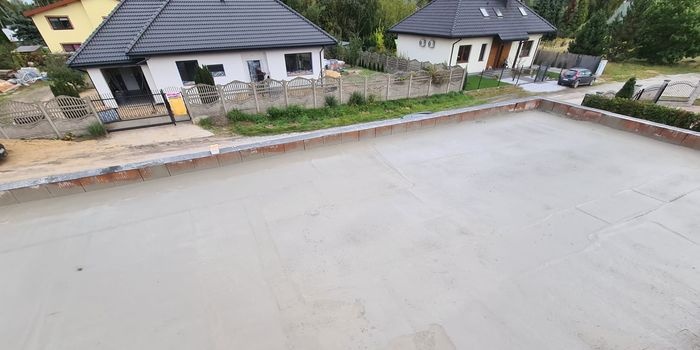
Poznaj innowacyjne, specjalistyczne produkty nadające przegrodom budowlanym odpowiednią trwałość, izolacyjność cieplną i szczelność. Jakie rozwiązania pozwolą nowe oraz remontowane chronić budynki i konstrukcje?
Poznaj innowacyjne, specjalistyczne produkty nadające przegrodom budowlanym odpowiednią trwałość, izolacyjność cieplną i szczelność. Jakie rozwiązania pozwolą nowe oraz remontowane chronić budynki i konstrukcje?
STYROPMIN Styropmin XPS PRO – niezawodny do zadań specjalnych
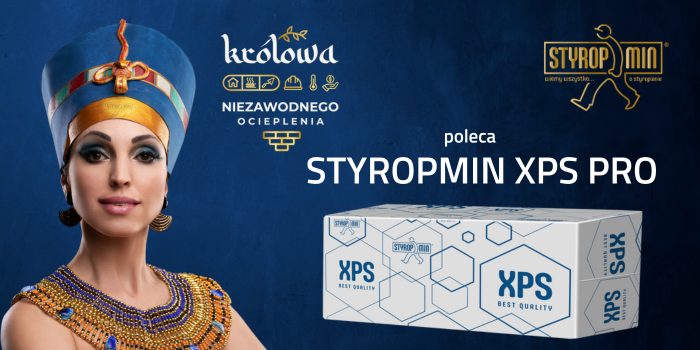
XPS PRO jest najnowszym osiągnięciem ekspertów z firmy Styropmin w dziedzinie skutecznej termoizolacji. To polistyren ekstrudowany, materiał bardziej wytrzymały i twardszy od uniwersalnego styropianu....
XPS PRO jest najnowszym osiągnięciem ekspertów z firmy Styropmin w dziedzinie skutecznej termoizolacji. To polistyren ekstrudowany, materiał bardziej wytrzymały i twardszy od uniwersalnego styropianu. Niezawodny w miejscach trudnych do ocieplenia, z ryzykiem zawilgocenia i dużą amplitudą temperatur, a także narażonych na duże naprężenia ściskające.
O czym przeczytasz w artykule:
|
W artykule scharakteryzowano bentonit, wymieniono obszary jego zastosowania oraz podano najważniejsze cechy. Przedstawia również zasady prawidłowej aplikacji materiałów bentonitowych. Materials used for the secondary waterproofing of buildings – bentonite materialsThe article characterizes bentonite, lists the areas of its application and its most important features. The principles of proper application of bentonite materials were also provided. |
Bentonit to naturalnie występujący, silnie pęczniejący minerał, który powstał w wyniku wietrzenia z kwaśnego popiołu wulkanicznego, i nawet w cienkiej warstwie ma silne działanie uszczelniające. Głównym składnikiem bentonitu jest minerał ilasty: montmorylonit. Bentonit z minerałów ilastych został tak nazwany na cześć miejsca, w którym został znaleziony (w pobliżu Fortu Benton w amerykańskim stanie Wyoming) w 1898 r. przez amerykańskiego geologa W.C. Knighta [2, 3].
Bentonit jest powszechnie stosowany w takich obszarach jak [2]:
- budownictwo,
- przemysł spożywczy,
- przemysł farmaceutyczny,
- przemysł ceramiczny,
- rolnictwo,
- przemysł papierniczy,
- przemysł metalowy,
- składowiska odpadów (materiały pokrywające).
Zastosowanie bentonitu sodowego jako materiału uszczelniającego wynika ze specyficznych właściwości tego minerału w odniesieniu do absorpcji wody. Zarówno naturalny, jak i sztucznie wytworzony bentonit sodowy pęcznieje, pochłaniając wodę, a gdy następuje jego wysychanie, pojawiają się pęknięcia (FOT. 1 na górze). Wynika to z obecności bardzo małych cząstek, które zwiększają powierzchnię.
Nagromadzenie cząsteczek wody (bentonit może jej związać od pięciu do siedmiu razy więcej niż wynosi jego ciężar) prowadzi do dziesięciokrotnego, a nawet piętnastokrotnego wzrostu objętości. Po zakończeniu procesu pęcznienia wewnątrzkrystalicznego wszystkie pory w warstwach bentonitu wypełnione są wodą, dzięki czemu transport wody ogranicza się wówczas do procesów przepływowych. W ten sposób z suchego bentonitu powstaje żelowa powłoka bentonitowa, natomiast efektem pęcznienia jest uszczelnienie bentonitu (współczynnik filtracji k ≤ 10–10 m/s [4]) – jeśli pęcznienie następuje w ograniczonej przestrzeni (bentonit jest „ściskany” między uszczelnianą przegrodą a przepuszczalną dla wody włókniną, warstwami ochronnymi lub gruntem), pojawia się ciśnienie pęcznienia (do 0,2 MPa), które zapobiega dalszej penetracji wody.
Nacisk musi być zagwarantowany na całej powierzchni, tak aby bentonit nie mógł „migrować” do zagłębień podczas procesu pęcznienia (samo zasypanie wykopu gruntem nie zapewnia wymaganego docisku). Im większy jest docisk, tym mniejsza przepuszczalność wody. Nie można jednak założyć, że zastosowanie bentonitu całkowicie uniemożliwi przenikanie wody [2, 3, 5, 6]. Po nawodnieniu wzrasta również przyczepność bentonitów do materiałów takich jak kamień, beton czy stal [4].
Warstwy uszczelniające z bentonitu mają w stosunku do elastycznych izolacji bitumicznych lub z tworzyw sztucznych czy też sztywnych izolacji mineralnych tę zaletę, że niewielkie uszkodzenie warstwy uszczelniającej, dzięki stale działającemu ciśnieniu pęcznienia, samoczynnie się uszczelnia, a występujące naprężenia, pęknięcia i ruchy są pochłaniane lub zamykane. Właściwość tę określa się jako zdolność samouszczelniania (RYS. 1), a jej konsekwencją jest również możliwość uszczelnienia niewielkich zarysowań podłoża [2, 3, 5].
Stałe ciśnienie pęcznienia powinno również zapobiegać penetracji wilgoci między warstwą uszczelnienia a podłożem, co również stanowi znaczną przewagę nad hydroizolacyjnymi materiałami rolowymi (w przypadku wystąpienia przecieku, stosunkowo łatwo jest go zlokalizować, ponieważ znajduje się on zazwyczaj w pobliżu wizualnie rozpoznawalnego miejsca penetracji wilgoci) [2]. Jednak te pozytywne właściwości występują jedynie wówczas, gdy bentonit pozostaje wilgotny (utrzymywany w stanie wilgotnym i zabezpieczony przed wysychaniem), dlatego też izolacje bentonitowe spełniają swoją rolę jedynie w środowisku ciągłego zawilgocenia. W strefie wysychania i zawilgacania bentonitu izolacja przez pewien czas przed ponownym spęcznieniem nie spełnia roli izolacji przeciwwodnej (czas ponownego spęcznienia po wyschnięciu jest stosunkowo długi) [3, 6].
W przeciwieństwie do wodoodpornych materiałów uszczelniających stopień wodoszczelności „hydroizolacji bentonitowych” zależy nie tylko od parametrów samego materiału, ale także od innych warunków brzegowych. Na pęcznienie i skurcz bentonitu mają na przykład wpływ stężenia soli obecnych w gruncie – wraz ze wzrostem stężenia soli zdolność pęcznienia (przy tej samej zawartości wody) zmniejsza się, co prowadzi do większego ryzyka uszkodzenia. W związku z tym na etapie projektowania hydroizolacji bentonitowych należy sprawdzić jakość wody i na tej podstawie określić właściwości uszczelniające bentonitu oraz ciśnienia pęcznienia [2, 3], lub też stosować materiały bentonitowe z dodatkiem polimerów zwiększających odporność na działanie soli [4].
Ponieważ działanie uszczelniające związane jest z ciśnieniem pęcznienia, które z kolei wymaga stałego dostępu wody, hydroizolacje bentonitowe z reguły mogą być stosowane wyłącznie w obszarze działania wody pod ciśnieniem. Z tego samego powodu hydroizolację bentonitową należy w zasadzie zawsze układać od strony wody [2].
Materiały bentonitowe przeznaczone do zastosowania jako element hydroizolacji budynków powinny spełniać następujące wymagania [2, 3]:
- dobra zdolność wchłaniania wody,
- zdolność pęcznienia wewnątrzkrystalicznego,
- wysoka zawartość montmorylonitu (> 70%), co skutkuje wysoką zdolnością adsorpcji,
- odporność na substancje występujące w gruncie,
- długotrwała trwałość.
Wysoka zawartość montmorylonitu (Al2(OH)2[Si205]2 · 4H2O) jest niezbędna do adsorpcji. Montmorylonity to zaliczane do minerałów ilastych tzw. krzemiany o budowie warstwowej: dwie warstwy tetraedryczne i jedna oktaedryczna (RYS. 2) – powierzchnia właściwa montmorylonitu jest wyjątkowo duża i warunkuje zdolność chłonięcia wody i pęcznienia w wyniku zwiększania odległości międzypakietowej (od 96 do 210 nm) [7, 8].
Nieprzepuszczalne dla wody właściwości bentonitu wynikają ze złożonego oddziaływania ww. właściwości. W budownictwie bentonit stosuje się do uszczelniania spoin, zarówno w nowo powstających konstrukcjach betonowych, jak i w miejscach połączenia nowych elementów z istniejącymi (RYS. 3), do uszczelniania ubytków, jak również jako hydroizolacje poziome oraz pionowe (w tym drugim przypadku również w budynkach istniejących) [2].
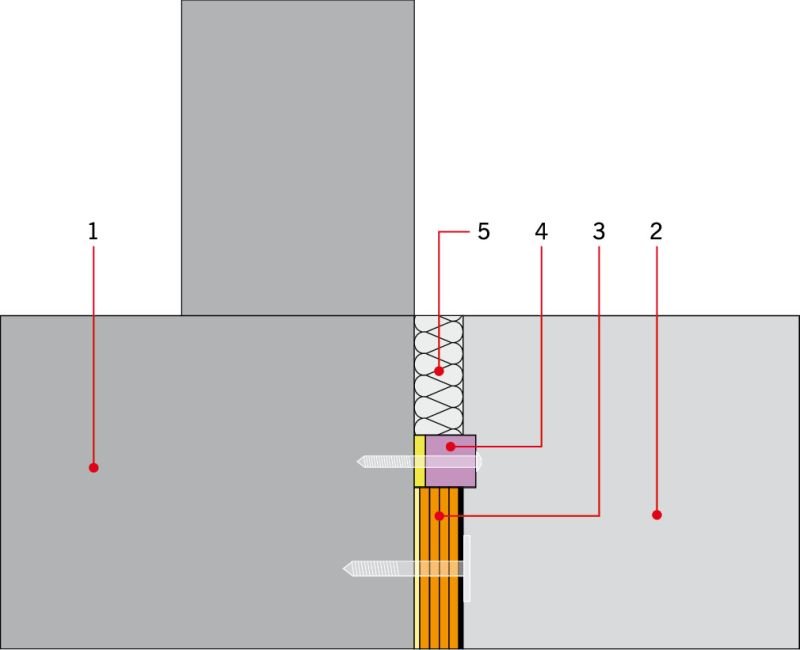
RYS. 3. Przykład uszczelnienia połączenia między istniejącym a powstającym budynkiem przy zastosowaniu materiałów bentonitowych. Objaśnienia: 1 – istniejąca konstrukcja, 2 – nowa konstrukcja, 3 – ułożona warstwowo mata bentonitowa, 4 – bentonitowa taśma pęczniejąca, 5 – wypełnienie dylatacji (materiał trwale elastyczny); rys.: [5]
Izolacyjne materiały bentonitowe występują w postaci paneli, membran, mat, taśm lub luźnego granulatu [5]. Obecnie dostępne maty bentonitowe mają grubość od ok. 2 do 10 mm. Oparte na materiałach bentonitowych rozwiązania stosowane w budynkach nowo wznoszonych potocznie określa się (z uwagi na kolor materiałów) „brązową wanną” [2].
Najstarszym wstępnie konfekcjonowanym wyrobem bentonitowym są panele, czyli tektura falista wypełniona granulatem bentonitowym. Tektura służy w tym wypadku jedynie jako płyta nośna dla granulatu (w późniejszym ukresie ulega ona biodegradacji). Panele mogą być dodatkowo pokryte powłoką opóźniającą dostęp wody lub posiadać zwiększoną odporność na zanieczyszczenia wody. Przy wznoszeniu nowych budynków panele mogą stanowić podkład pod płytę fundamentową zastępujący podkład z chudego betonu. W przypadku wykonywania izolacji pionowych panele mocuje się mechanicznie (prace można prowadzić w dowolnej temperaturze otoczenia). Konieczne jest odpowiednie przygotowanie podłoża (nie jest wymagane jego gruntowanie) oraz zachowanie minimalnych zakładek. Szczególną uwagę należy zwrócić na odpowiednie mocowanie w celu uniknięcia powstawania pustek powietrznych oraz zachowania krawędzi uszczelnienia [5]. Paneli bentonitowych nie należy stosować przy ciśnieniu wody przekraczającym 0,1 MPa.
Do uszczelnienia poza obszarem występowania wody napierającej (przy ciśnieniu nieprzekraczającym 0,45 MPa) przewidziane są również membrany bentonitowe składające się z folii z tworzywa sztucznego, bentonitu i rozpuszczalnej w wodzie membrany ochronnej (RYS. 4).
Membrany przykleja się lub też mocuje mechanicznie do podłoża, zachowując minimalne zakłady. Jedynie dla celów montażowych miejsca styku okleja się paskami folii – laminaty foliowe (z uwagi na nieszczelne szwy) nie stanowią warstwy uszczelniającej [5].
Maty bentonitowe oznaczane w normach symbolem GBR-C (geosyntetyczna bariera iłowa) są rodzajem kompozytu, tj. wyrobem wytwarzanym z jednego lub więcej geosyntetyków i pęczniejącego iłu – ich elementami są [4–6]:
- geotkanina lub geowłóknina (górna warstwa),
- sproszkowany lub zgranulowany bentonit, względnie włóknina o luźnej strukturze wypełniona bentonitem (środkowa warstwa),
- geowłóknina (dolna warstwa).
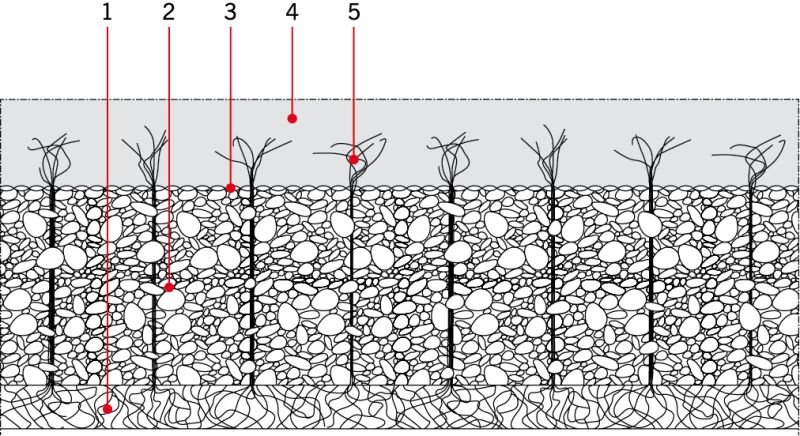
RYS. 5. Bentonitowa mata igłowana. Objaśnienia: 1 – włóknina PP, 2 – granulowany bentonit, 3 – tkanina PP, 4 – beton, 5 – włókna zapewniające przyczepność; rys.: B. Monczyński
Poszczególne warstwy zostają zespolone w jednorodny produkt w procesie igłowania, który polega na zaczepieniu specjalnymi igłami włókien ze spodniej włókniny i przeciągnięciu ich poprzez warstwę bentonitu poza tkaninę. Uzyskuje się dzięki temu wzajemne powiązanie, zamknięcie oraz ściśnięcie granulatu między wzajemnie powiązanymi warstwami geotkanin (RYS. 5, FOT. 2–4) [5].
Do produkcji mat wykorzystuje się głównie bentonity sodowe, ale również wapniowe, wapniowe aktywowane lub też sodowe modyfikowane chemicznie. Stosowane są bentonity w postaci proszku lub drobnych granulek, o wilgotności 5–15%, w ilości od 3 do 6 kg na 1 m2 gotowego wyrobu [4, 6].
Maty bentonitowe charakteryzują się wysoką elastycznością, odpornością na przebicie oraz przyczepnością do podłoża (muszą być jednak trwale do niego dociśnięte). Na powierzchniach poziomych maty układa się luźno na podłożu, przy czym można to zrobić bezpośrednio na warstwie podsypki (z pominięciem chudego betonu). Na powierzchniach pionowych przybija się gwoździami do betonu lub przystrzeliwuje osadzakiem. Istnieje również możliwość montowania maty wewnątrz deskowania lub do stałej obudowy wykopu [5].
Maty bentonitowe mogą być stosowane do wykonywania izolacji przeciwwodnych, zarówno poziomych, jak i pionowych [6]. Materiał ten uwzględniono w normie PN-EN 13491 „Bariery geosyntetyczne – Właściwości wymagane w odniesieniu do wyrobów stosowanych do budowy tunelów i towarzyszących im budowli podziemnych” [10]. Zalecane, a wymagające badań, właściwości użytkowe mat bentonitowych podano w TABELI.
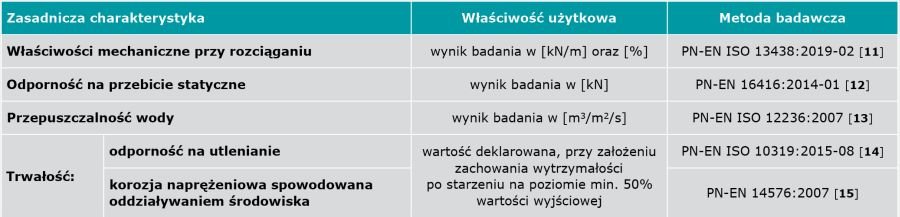
TABELA. Zestawienie zasadniczych charakterystyk i odpowiadających im właściwości użytkowych dla mat bentonitowych GBR-C [10] według [4]
Wykonując hydroizolację z mat bentonitowych, należy się stosować do następujących zasad [2, 5, 6]:
- Podłoże pod hydroizolację powinno być odpowiednio zagęszczone, równe, pozbawione gruzu, korzeni, ostrych kamieni, lodu i stojącej wody.
- Materiał należy układać w taki sposób, aby pomiędzy poszczególnymi matami zachować zakład o szerokości nie mniejszej niż 10–15 cm; w strefie zakładu, po wcześniejszym usunięciu z niej wszelkich zanieczyszczeń, nanosi się ciągłą warstwę granulatu bentonitowego.
- Matę należy układać w taki sposób, aby jej krawędzie były rozprostowane, pozbawione zmarszczeń oraz zagięć.
- Mata powinna być rozwijana od punktu najwyższego do najniższego, w taki sposób, aby nie dopuścić do jej napięcia lub naprężenia, oraz unikając powstawania zagięć, zmarszczek lub „rybich ust” na jej brzegach.
- Górne krawędzie maty należy zamocować liniowo przy użyciu listew/profili metalowych lub plastikowych oraz uszczelnić szpachlą bentonitową, a także zapewnić co najmniej 10–15 cm zakładu z izolacją strefy cokołowej budynku (RYS. 6).
- Warstwę ochrony mechanicznej należy wykonać z płyty pilśniowej lub płyt z polistyrenu ekstrudowanego.
- Na powierzchniach poziomych maty należy układać pasmami w układzie schodkowym – izolacja powinna być wykonywana pod płytą żelbetową, o grubości nie mniejszej niż 15 cm.
- Mat bentonitowych nie należy stosować w strefie przemarzania – odcinek przemarzania należy zabezpieczyć hydroizolacją kompatybilną z matą bentonitową.
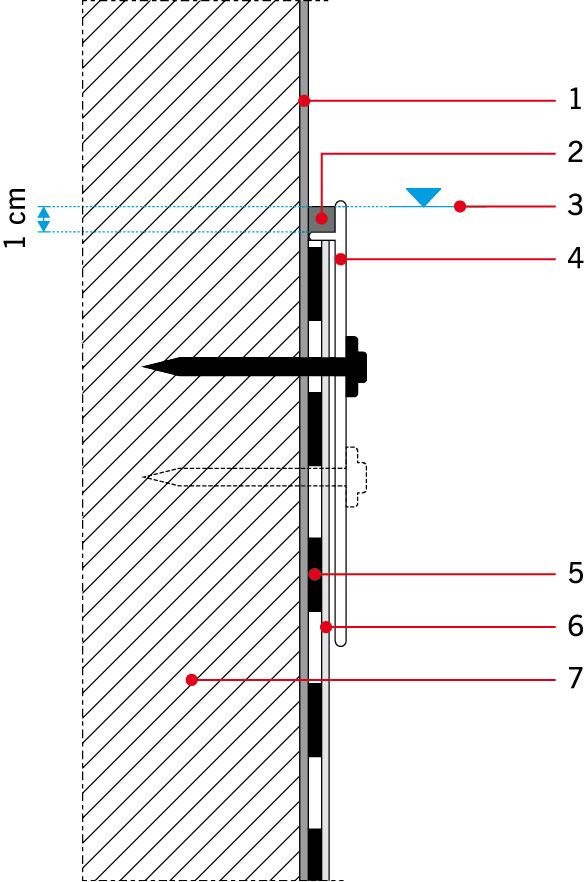
RYS. 6. Zakończenie górnej krawędzi uszczelnienia bentonitowego. Objaśnienia: 1 – hydroizolacja powłokowa (np. PMBC) – zakład minimum 30 cm, 2 – szpachla bentonitowa, 3 – górny poziom uszczelnienia bentonitowego: co najmniej 30 cm powyżej maksymalnego poziomu wód gruntowych, 4 – profil aluminiowy lub z tworzywa sztucznego, 5 – mata bentonitowa, 6 – warstwa ochronna, 7 – izolowane podłoże; rys.: [5]
Aby zapewnić wystarczające ciśnienie pęcznienia, konieczne jest wbudowanie materiałów bentonitowych w stanie niespęcznionym (suchym). Do czasu zakończenia prac (włącznie z zasypaniem wykopu) bentonit nie może być narażony na działanie wilgoci, ponieważ natychmiast spowodowałoby to przedwczesne rozpoczęcie procesu pęcznienia. Pewien stopień ochrony przed przedwczesną aktywacją procesu pęcznienia może zapewnić zastosowanie rozpuszczalnej w wodzie folii ochronnej. Jeśli jednak spodziewane są dłuższe przerwy w pracy, wbudowane maty bentonitowe należy odpowiednio zabezpieczyć przed działaniem wody [2].
W przeciwieństwie do innych materiałów uszczelniających, hydroizolacje bentonitowe można natomiast montować niemalże niezależnie od warunków atmosferycznych. Również wymagania dotyczące przygotowania podłoża są znacznie niższe – oprócz oczyszczenia podłoża należy usunąć wystające elementy, zniwelować większe zagłębienia oraz wyokrąglić lub sfazować ostre krawędzie. Gruntowanie lub inne tego typu przygotowania podłoża także nie są wymagane. Większego znaczenia nie odgrywa również wilgotność uszczelnianego podłoża.
W celu zapewnienia odpowiednich warunków pęcznienia (docisku) niektóre systemy hydroizolacji bentonitowych mogą być układane etapami (z odcinkowym wypełnianiem wykopu). Przejścia instalacyjne w nowym budownictwie uszczelniane są bentonitową taśmą pęczniejącą [2].
Dzięki zdolności bentonitu do pęcznienia, stosunkowo łatwo zapewnić szczelne połączenie z innymi izolacjami, np. w nowym i istniejącym budynku. Przy wystarczającej długości zakładu między izolacją istniejącą a bentonitową nie istnieje ryzyko niekontrolowanego wydostawania się wody poza poziom uszczelnienia.
Możliwe jest również wykonanie połączenia uszczelniającego w strefie wody napierającej bez konieczności zastosowania kosztownych konstrukcji z kołnierzy zaciskowych [5].
W momencie zakopania wykopu materiały bentonitowe zostają wystawione na działanie wilgoci, która uruchamia proces pęcznienia. Stopień szczelności materiału zależy od stopnia pęcznienia oraz od nacisku kontaktowego.
Od pewnego czasu dostępne są również maty z wierzchnią warstwą z folii rozpuszczalnych w wodzie, które nieco opóźniają, a tym samym kontrolują proces pęcznienia bentonitu [3].
Literatura
1. B.J. Rouba, „Pielęgnacja świątyni i innych zabytków. Książka nie tylko dla księży”, Wydawnictwo Naukowe Uniwersytetu Mikołaja Kopernika, Toruń 2014.
2. U. Wild, „Nachträgliche Vertikalabdichtung” in „Bauwerksabdichtung in der Altbausanierung – Verfahren und juristische Betrachtungsweise”, J. Weber, V. Hafkesbrink. Eds., Springer Vieweg, Wiesbaden 2018, pp. 305–393.
3. F. Frössel, „Mauerwerkstrockenlegung und Kellersanierung. Wenn das Haus nasse Füße hat 3”, vollst ed.: Fraunhofer IRB Verlag, Stuttgart 2012.
4. B. Francke, „Nowoczesne hydroizolacje budynków, Zeszyt 1. Zabezpieczenia wodochronne części podziemnych budynków”, Wydawnictwo Naukowe PWN, Warszawa 2021.
5. R. Ruhnau, „Abdichtung mit Bentonit” in „Lufsky Bauwerksabdichtung”, Teubner, Wiesbaden 2006, pp. 249–264.
6. B. Francke, „Warunki Techniczne Wykonania i Odbioru Robót Budowlanych. Część C: Zabezpieczenia i izolacje. Zeszyt 5: Izolacje przeciwwilgociowe i wodochronne części podziemnych budynków”, Instytut Techniki Budowlanej, Warszawa 2019.
7. O. Henning, D. Knöfel, „Baustoffchemie”, Verlag Bauwesen, Berlin 2002. Available: 3-345-00799-1.
8. L. Czarnecki et al., „Chemia w budownictwie”, Arkady, Warszawa 1996.
9. M. Cholewa et al., „Wielkość przecieków przez uszkodzenia maty bentonitowej (GBR-C) przy zmiennych wysokościach słupa wody”, „IZOLACJE” 9/2015, s. 54–58.
10. PN-EN 13491:2018-04, „Bariery geosyntetyczne – Właściwości wymagane w odniesieniu do wyrobów stosowanych do budowy tunelów i towarzyszących im budowli podziemnych”.
11. PN-EN ISO 13438:2019-02, „Geosyntetyki – Selekcyjna metoda wyznaczania odporności geotekstyliów i wyrobów pokrewnych na utlenianie”.
12. PN-EN 16416:2014-01, „Geosyntetyczne bariery iłowe – Oznaczenie wskaźnikowego natężenia przepływu wody – Metoda parametru o podatnej ściance przy stałym ciśnieniu hydrostatycznym”.
13. PN-EN ISO 12236:2007, „Geosyntetyki – Badanie statycznego przebicia (metoda CBR)”.
14. PN-EN ISO 10319:2015-08, „Geosyntetyki – Badanie wytrzymałości na rozciąganie metodą szerokich próbek”.
15. PN-EN 14576:2007, „Geosyntetyki – Metoda wyznaczania odporności polimerowych barier geosyntetycznych na korozję naprężeniową spowodowaną wpływem środowiska”.