Szacowanie wytrzymałości na ściskanie betonu elementów wykonanych na budowie
Estimation of the concrete compression strength of elements made on the site

Jaką wytrzymałość mają elementy betonowe wykonane na budowie? fot. K. Pogan
Dynamiczne wykorzystanie betonu nastąpiło w wieku XIX, od momentu opracowania w roku 1824 przez Aspdina technologii sztucznego spoiwa, które nazwał cementem portlandzkim. Dzisiaj pojęcie betonu jest znacznie szersze i uległo wielu modyfikacjom.
Zobacz także
mgr inż. Bartosz Witkowski, prof. dr hab. inż. Krzysztof Schabowicz, mgr inż. Mateusz Moczko Izolacje we współczesnej prefabrykacji betonowej
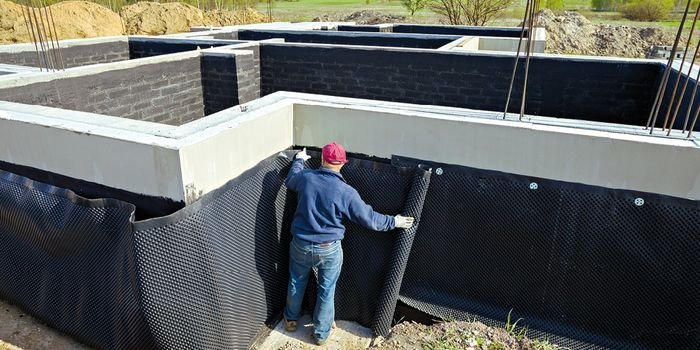
Idea prefabrykacji w budownictwie sięga czasów rzymskich, kiedy to przy wykorzystaniu wapna, gipsu, wody, kamiennego kruszywa oraz popiołu wulkanicznego produkowano kompozyt przypominający dzisiejszy beton....
Idea prefabrykacji w budownictwie sięga czasów rzymskich, kiedy to przy wykorzystaniu wapna, gipsu, wody, kamiennego kruszywa oraz popiołu wulkanicznego produkowano kompozyt przypominający dzisiejszy beton. Kolejnym krokiem w historii nawiązującym do prefabrykacji było wynalezienie współczesnego betonu z cementu portlandzkiego w 1824 r. i początki stosowania żelbetu do produkcji siatkobetonowych donic [1].
Bostik Bostik AQUASTOPP – szybkie i efektywne rozwiązanie problemu wilgoci napierającej
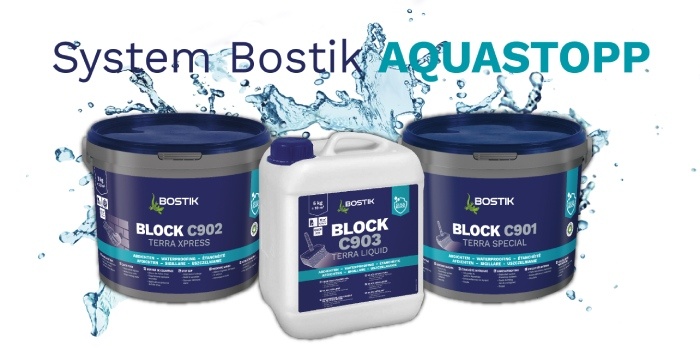
Bostik to firma z wieloletnią tradycją, sięgającą 1889 roku, oferująca szeroką gamę produktów chemii budowlanej dla profesjonalistów i majsterkowiczów. Producent słynie z innowacyjnych rozwiązań i wysokiej...
Bostik to firma z wieloletnią tradycją, sięgającą 1889 roku, oferująca szeroką gamę produktów chemii budowlanej dla profesjonalistów i majsterkowiczów. Producent słynie z innowacyjnych rozwiązań i wysokiej jakości preparatów, które znajdują zastosowanie w budownictwie, przemyśle i renowacji.
RAXY Sp. z o.o. Nowoczesne technologie w ciepłych i zdrowych budynkach
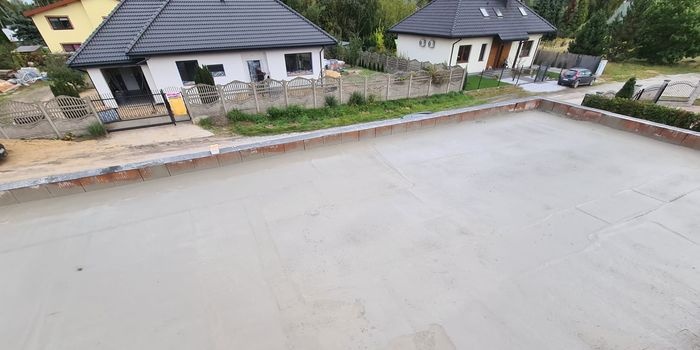
Poznaj innowacyjne, specjalistyczne produkty nadające przegrodom budowlanym odpowiednią trwałość, izolacyjność cieplną i szczelność. Jakie rozwiązania pozwolą nowe oraz remontowane chronić budynki i konstrukcje?
Poznaj innowacyjne, specjalistyczne produkty nadające przegrodom budowlanym odpowiednią trwałość, izolacyjność cieplną i szczelność. Jakie rozwiązania pozwolą nowe oraz remontowane chronić budynki i konstrukcje?
Obecnie beton uzyskuje się nie tylko z okruchów skalnych (kruszywo naturalne lub łamane), ale także z kruszywa sztucznego i wypełniaczy, zaś zamiast cementu stosuje się inne spoiwa, a jego właściwości wzbogaca się domieszkami i dodatkami.
Beton można ogólnie zdefiniować jako materiał budowlany uzyskany z połączenia wypełniacza spoiwem. Tak uzyskany materiał nosi nazwę kompozytu, w którym zaczyn spełnia rolę matrycy, a kruszywo inkluzji.
O czym przeczytasz w artykule:
|
Podczas wykonywania elementów betonowych warunki zewnętrzne mają ważny wpływ na uzyskanie zakładanych parametrów końcowych. Przede wszystkim wytrzymałość na ściskanie i trwałość są najistotniejsze. W opisywanym przypadku mamy do czynienia z obniżeniem wytrzymałości na ściskanie i powstaniem rys i spękań elementów betonowych wywołanych wysoką temperaturą podczas betonowania i niewłaściwą pielęgnacją. Aby oszacować faktyczną wytrzymałość na ściskanie betonu w elementach wykonano badania nieniszczące, mierząc liczbę odbicia. Wcześniej, wyskalowano młotek Schmidta znajdując zależność wytrzymałości na ściskanie i liczby odbicia.
Estimation of the concrete compression strength of elements made on the site External conditions during the construction of concrete elements strongly influence the achievement of the intended final parameters. First of all, it refers to their compressive strength and durability, which are most important. In this case, the compression strength is reduced and cracks and cracks in the concrete elements appear due to high temperature during concrete pouring and improper maintenance. In order to estimate the actual compression strength of concrete in the elements, non-destructive testing was carried out by measuring the rebound number. Beforehand, the Schmidt hammer was calibrated in order to find the dependence of compression strength and rebound number. |
Beton i stal są obecnie dwoma najbardziej powszechnie stosowanymi materiałami w konstrukcjach budowlanych. Czasem współpracują, tworząc żelbet, a czasem konkurują ze sobą w tym sensie, że konstrukcje podobnego typu i funkcji mogą być zbudowane z jednego z tych materiałów. A jednak inżynierowie zwykle wiedzą mniej o betonie, z jakiego jest wykonana konstrukcja, niż o stali.
Stal jest produkowana w warunkach dokładnie kontrolowanych, jej właściwości są określone w laboratorium i opisywane w świadectwach producenta. Projektant musi zatem jedynie wyspecyfikować stal zgodnie z odpowiednią normą, a nadzór inżyniera na budowie jest ograniczony do wykonawstwa połączeń między poszczególnymi elementami stalowymi.
Na budowie obiektu betonowego sytuacja jest całkowicie inna. Wprawdzie jakość cementu i kruszyw jest gwarantowana przez producenta w sposób podobny do tego jak w przypadku stali, jednak to beton, a nie cement i kruszywo jest materiałem konstrukcyjnym.
Elementy z betonu są wykonywane często na budowie, a ich jakość jest zależna niemal wyłącznie od fachowości wykonawstwa przy produkcji, transporcie, układaniu mieszanki betonowej oraz pielęgnowaniu świeżego betonu. W tym miejscu należy przytoczyć słowa prof. Adama Neville’a:
- „Nie należy obawiać się, że wykonanie dobrego betonu jest trudne. Zły beton – często materiał o niewygodnej konsystencji, twardniejący w porowatą, niejednorodną masę – jest po prostu wykonywany przez zmieszanie cementu, kruszywa i wody. Zadziwiające, że składniki dobrego i złego betonu są dokładnie takie same, a jedynie umiejętności, poparte przez zrozumienie wykonywanych czynności i zachodzących procesów, są odpowiedzialne za różnice”.
W tym miejscu należy podkreślić znaczenie i rolę pielęgnacji świeżego betonu, w kontekście omawianego przypadku była to bowiem główna przyczyna powstałego problemu.
Pielęgnacja świeżego betonu ma na celu:
- zapewnienie optymalnych warunków cieplno-wilgotnościowych w dojrzewającym betonie (wspomaganie procesu hydratacji cementu),
- ochronę świeżo wykonanego betonu przed szkodliwym wpływem promieni słonecznych, działaniem wiatru, opadów atmosferycznych,
- przeciwdziałanie skurczowi spowodowanego wysychaniem betonu,
- redukcję różnicy temperatury na powierzchni elementu betonowego i w jego wnętrzu (ograniczenie naprężeń termicznych i ryzyka spękania elementu),
- zapobieganie zamarzaniu wody zarobowej i zapewnienie prawidłowego rozwoju wytrzymałości betonu w warunkach obniżonej temperatury.
Wyróżnia się następujące metody pielęgnacji:
- pielęgnację na mokro – okrywanie wilgotnymi matami jutowymi lub geowłókniną – zraszanie zabezpieczonej powierzchni wodą,
- stosowanie osłon – okrywanie folią lub płytami z materiałów izolacyjnych (wełna mineralna, styropian), wykonanie namiotu ochronnego w miejscu wbudowywania betonu,
- stosowanie preparatów do pielęgnacji betonu – pokrywanie powierzchni świeżego betonu odpowiednimi preparatami ograniczającymi odparowanie wody z powierzchni i odbijającymi promieniowanie słoneczne.
Minimalny, zalecany czas pielęgnacji świeżego betonu, w zależności od rodzaju cementu i warunków atmosferycznych, podany został w TABELI.
Należy także zaznaczyć, że brak pielęgnacji lub niewłaściwa pielęgnacja powoduje, że powierzchnia betonu będzie osłabiona, a struktura betonu będzie wykazywać zarysowania. Wpłynie to negatywnie na trwałość betonu i konstrukcji.
Zabiegi pielęgnacyjne są etapem postępowania z mieszanką betonową i świeżym betonem równie ważnym jak projektowanie składu mieszanki z uwzględnieniem aspektów trwałości, dobór odpowiednich składników, mieszanie i transport na miejsce wbudowania, układanie i zagęszczanie mieszanki betonowej. Od tego etapu także zależeć będzie dalsza obróbka powierzchni i jej przygotowanie pod nakładanie powłok ochronnych, co w konsekwencji przekłada się na skuteczność zabezpieczenia antykorozyjnego powierzchni betonowych czy ewentualnych napraw.
W omawianym przypadku wykonywano żelbetowe stopy fundamentowe pod słupy hali produkcyjno-magazynowej. Betonowanie odbywało się podczas letnich upałów, gdzie temperatura powietrza w ciągu dnia przekraczała 30°C.
Podczas wizji lokalnych zaobserwowano liczne spękania powierzchni betonu na powierzchniach poziomych fundamentów żelbetowych – powierzchnie górne fundamentów (FOT. 1–2), a także odsadzki (FOT. 3–4).

FOT. 4. Rysy widoczne poprzez warstwę mineralnego zabezpieczenia powierzchniowego na odsadzce fundamentu betonowego; fot.: K. Pogan

FOT. 5. Widoczne rysy na powierzchni fundamentu betonowego w okolicy kotew stalowych; fot.: K. Pogan

FOT. 6. Widok spękań fundamentu betonowego przykryty warstwą bitumicznego zabezpieczenia powierzchniowego; fot.: K. Pogan
Na uwagę zasługują również pęknięcia występujące w bliskim sąsiedztwie kotew stalowych osadzonych w fundamentach (FOT. 5). Na części fundamentów nałożono już izolację bitumiczną, również na powierzchniach poziomych – odsadzki, gdzie występują spękania (FOT. 6).
Zaobserwowano, że niektóre fundamenty po rozdeskowaniu, w trzecim dniu od betonowania, pozostawione zostały bez odpowiedniej ochrony przed przesychaniem i pozbawione były odpowiedniej pielęgnacji (FOT. 7–8).

FOT. 8. Częściowo rozszalowany fundament betonowy, pozostawiony bez dalszej pielęgnacji; fot.: K. Pogan
Pojawiają się zatem dwa problemy do rozwiązania.
- Po pierwsze – ze względu na warunki dojrzewania w temperaturze ok. 30°C, dodatkowo bez właściwej pielęgnacji, wytrzymałość na ściskanie betonu fundamentów może nie osiągnąć wartości przyjętych do obliczeń statycznych przez projektanta.
- Po drugie – wyraźne rysy zagrażają trwałości elementów żelbetowych, poddanych podczas eksploatacji oddziaływaniu wilgoci i kwasów humusowych z gruntu.
Dla oceny betonu fundamentów wykonano odwierty koronką diamentową o średnicy zewnętrznej 102 mm i w ten sposób pobrano z wytypowanych fundamentów próbki (FOT. 9–10) przeznaczone do określenia wytrzymałości na ściskanie w próbie bezpośredniego ściskania (zgodnie z normą PN-EN 12504-1) [1].

FOT. 9. Wykonywanie odwiertu w fundamencie betonowym w celu pobrania próbek do badań wytrzymałości na ściskanie; fot.: K. Pogan
Dodatkowo dokonano pomiaru liczby odbicia młotkiem Schmidta dla wybranych fundamentów w celu oszacowania metodą nieniszczącą wytrzymałości na ściskanie (zgodnie z normą PN-EN 12504-2) [2].
Do bezpośredniego ściskania przeznaczono próbki o średnicy 94,2 mm i stosunku średnicy do wysokości 1,0 z pobranych odwiertów, po dwie z górnej powierzchni i po dwie z warstwy głębszej (na poziomie 12–25 cm od powierzchni górnej fundamentu) z dwóch wytypowanych fundamentów (FOT. 11).
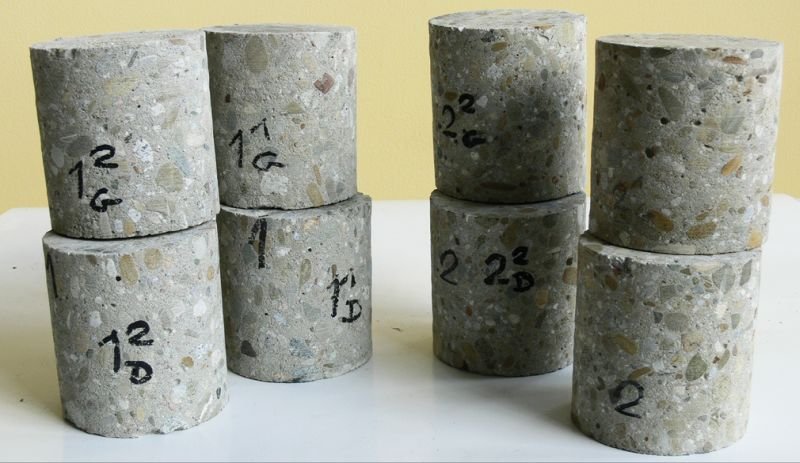
FOT. 11. Sformatowane próbki betonu pobrane z fundamentów, przygotowane do badań wytrzymałości na ściskanie; fot.: K. Pogan
Podczas próby ściskania bezpośredniego wykonano także pomiar liczby odbicia młotkiem Schmidta, aby wyznaczyć zależność między wytrzymałością na ściskanie i liczbą odbicia, tzw. skalowanie młotka Schmidta (zgodnie z Instrukcją ITB nr 210).
Ze względu na zróżnicowany wiek betonu fundamentów w dniu badania wytrzymałości na ściskanie pobranych próbek, w zależności od lokalizacji fundamentu – odpowiednio 22 i 14 dni oraz biorąc pod uwagę warunki dojrzewania betonu na budowie, można przyjąć, że określona w próbie bezpośredniego ściskania wytrzymałość jest na poziomie 0,85 wytrzymałości 28-dniowej, miarodajnej do oszacowania klasy wytrzymałości betonu [3, 4].
Równocześnie dla określenia klasy wytrzymałości betonu przyjęto następujące kryterium kwalifikacyjne [5–8]:
ƒc min ≥ α ƒck (1)
gdzie:
ƒc min – minimalna wytrzymałość na ściskanie uzyskana podczas próby ściskania bezpośredniego n próbek, MPa,
ƒck – odpowiadająca danej klasie wytrzymałościowej betonu wytrzymałość charakterystyczna, MPa,
α – współczynnik zależny od liczby n badanych próbek, dla n = 3–4 α = 1,15.
Jeśli powyższy warunek nie jest spełniony, można posłużyć się innym kryterium, wówczas równocześnie muszą zostać spełnione dwa warunki:
ƒc min ≥ ƒck (2)
ƒc śr ≥ 1,2 ƒck (3)
Biorąc pod uwagę wyniki otrzymane w bezpośredniej próbie ściskania oraz zgodnie z przytoczonymi wyżej kryteriami, można oszacować klasę wytrzymałości betonu fundamentów.
Na podstawie pomiaru liczby odbicia oraz wyników badań niszczących (uwzględniających wiek badanego betonu) określono linię trendu opisującą zależność wytrzymałości na ściskanie od liczby odbicia.
Wykorzystując tę zależność wyznaczoną podczas badań niszczących, oszacowano wytrzymałość na ściskanie betonu wybranych fundamentów, gdzie dokonano badań nieniszczących, określając liczbę odbicia młotkiem Schmidta typu N.
Uwzględniając wyniki wizji lokalnych, dokumentacji fotograficznej, wykonanych badań niszczących i nieniszczących oraz analizy uzyskanych wyników, można stwierdzić, że beton fundamentów jest o niższej niż projektowana klasie wytrzymałości i ma osłabioną strukturę. Spękania występujące na powierzchniach poziomych fundamentów mają swoją przyczynę w warunkach dojrzewania betonu – wysoka temperatura otoczenia, niedostateczna pielęgnacja, a także, na co wskazują obniżenia poziomu – charakterystyczne wklęśnięcia powierzchni, prawdopodobnie wynikające ze zbyt dużej ilości wody w mieszance betonowej.
Obserwując przełom próbki po zniszczeniu podczas bezpośredniej próby ściskania (FOT. 12), można zauważyć wysuszoną strukturę betonu, łatwe odspajanie się ziaren kruszywa od matrycy cementowej, co świadczy o niskiej przyczepności i słabej współpracy między poszczególnymi fazami. Należy także zwrócić uwagę na stosunkowo małą zawartość kruszywa grubego w stosie okruchowym.
Powszechnie wiadomo, że istotny wpływ na wytrzymałość betonu mają warunki, w jakich przebiega jego dojrzewanie, zwłaszcza w początkowej fazie twardnienia. Z literatury budowlanej [6] oraz z doświadczenia wiadomo, że gdy przy starannej pielęgnacji (nawilżaniu betonu oraz osłonięciu go przed wysychaniem) przez okres 14 dni osiąga się 100% zakładanej wytrzymałości na ściskanie, to przy takiej pielęgnacji przez okres krótszy, np. 7 lub 2 dni albo w warunkach suchych, bez pielęgnacji beton osiąga poziom odpowiednio 95%, 85% i 50% wytrzymałości końcowej.
Występujące pęknięcia betonu, odzwierciedlające rysunek zbrojenia, wskazują nie tylko na osłabienie struktury samego betonu, ale również na zmniejszenie przyczepności prętów zbrojeniowych do betonu, dotyczy to również stalowych kotew. Jest to wynikiem wysokiej temperatury otoczenia podczas betonowania i pierwszej fazy dojrzewania betonu, co w połączeniu z niewystarczającą pielęgnacją oraz ze znaczną różnicą we współczynnikach rozszerzalności termicznej stali, kruszywa i zaczynu cementowego poskutkowało osłabieniem struktury i pogorszeniem przyczepności między poszczególnymi fazami.
Innym aspektem związanym z zaobserwowanymi uszkodzeniami betonu jest jego trwałość. Przez otwartą strukturę powierzchni betonu będzie możliwa penetracja wody w głąb fundamentu, a co za tym idzie stworzenie warunków do rozwoju korozji zbrojenia, co przy niskiej wytrzymałości na ściskanie betonu zagraża niezawodnej pracy fundamentu – jako podpory konstrukcji stalowej budowanej hali. Ostateczną decyzję dotyczącą podejmowania ewentualnych działań naprawczych należy skonsultować z biurem projektowym opracowującym projekt wykonawczy fundamentów lub właściwym rzeczoznawcą budowlanym.
Literatura
1. PN-EN 12504-1, „Badania betonu w konstrukcjach – Część 1: Próbki rdzeniowe – Pobieranie, ocena i badanie wytrzymałości na ściskanie”.
2. PN-EN 12504-2, „Badania betonu w konstrukcjach – Część 2: Badanie nieniszczące – Oznaczanie liczby odbicia”.
3. A.M. Neville, „Właściwości betonu”, wyd. IV, Polski Cement, Kraków 2000.
4. Z. Kurnik, „Materiały pomocnicze do ćwiczeń z technologii betonu”, Politechnika Krakowska, Kraków 1985.
5. J. Śliwiński, „Beton zwykły. Projektowanie i podstawowe właściwości”, Polski Cement, Kraków 1999.
6. Z. Jamrozy, „Beton i jego technologie”, PWN, Warszawa–Kraków 2000.
7. PN-EN/B-06250, „Beton zwykły”.
8. PN-EN 206, „Beton – Wymagania, właściwości, produkcja i zgodność”.