Warunki techniczne wykonania i odbioru warstw uszczelnienia z geomembranami
Cz. 2. Postępowanie na placu budowy
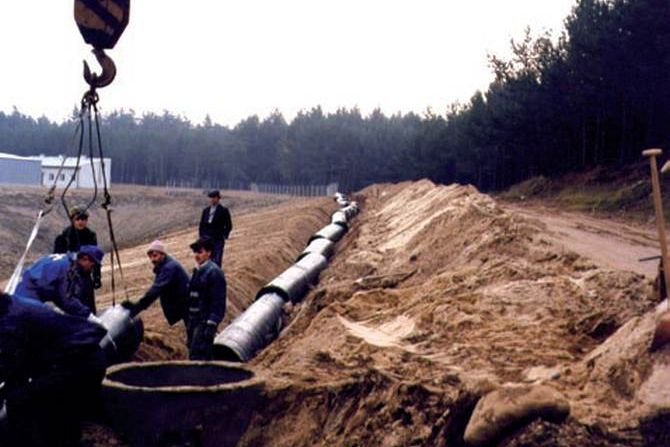
Archiwum autora
Składowiska odpadów komunalnych i przemysłowych, wylewiska nieczystości i substancji toksycznych oraz wszelkiego rodzaju zbiorniki ziemne, żelbetowe i stalowe są szczególną grupą obiektów, w których zastosowane geosyntetyki powinny podlegać surowemu reżimowi technologicznemu.
Zobacz także
Immergas Jaka jest średnia żywotność pompy ciepła?

Pompy ciepła to nowoczesny i ekologiczny sposób na ogrzewanie budynków. Z tego powodu coraz częściej wypierają węglowe lub gazowe kotły, które w przeciwieństwie do pomp powodują zanieczyszczenie powietrza....
Pompy ciepła to nowoczesny i ekologiczny sposób na ogrzewanie budynków. Z tego powodu coraz częściej wypierają węglowe lub gazowe kotły, które w przeciwieństwie do pomp powodują zanieczyszczenie powietrza. Wiele osób obawia się zmiany źródła ogrzewania m.in. ze względu na rzekomą niską trwałość pompy. Jaka jest przeciętna żywotność pompy ciepła, od czego zależy i jak ją zwiększyć?
LERG SA Lerg uruchomił nową instalację polioli
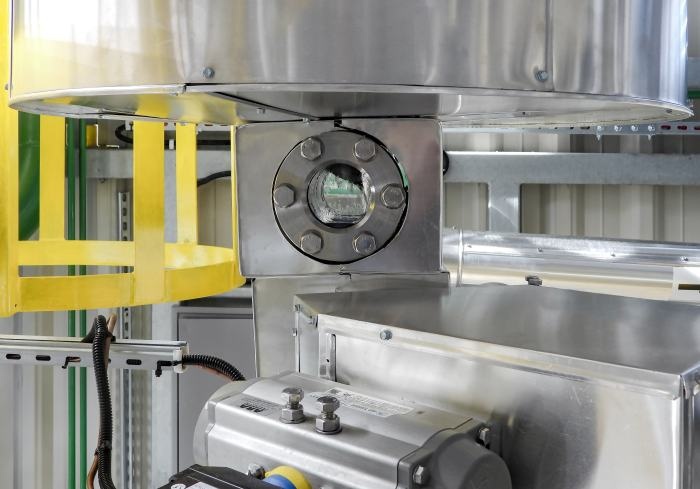
Rynek ociepleń poliuretanowych, w tym płyt warstwowych – stale się rozwija. Jest to spowodowane m.in. zwiększeniem świadomości ekologicznej wśród odbiorców. Stawiane przez Unię Europejską, wysokie wymagania...
Rynek ociepleń poliuretanowych, w tym płyt warstwowych – stale się rozwija. Jest to spowodowane m.in. zwiększeniem świadomości ekologicznej wśród odbiorców. Stawiane przez Unię Europejską, wysokie wymagania w zakresie bezpieczeństwa również wpływają na sprofesjonalizowanie rynku produktowego.
Gamrat Technologie wykorzystywane w produkcji rur

W nowoczesnym przemyśle i budownictwie rury odgrywają kluczową rolę w tworzeniu niezawodnych i trwałych systemów do przesyłu wody, ścieków oraz innych substancji. Technologie wykorzystywane w produkcji...
W nowoczesnym przemyśle i budownictwie rury odgrywają kluczową rolę w tworzeniu niezawodnych i trwałych systemów do przesyłu wody, ścieków oraz innych substancji. Technologie wykorzystywane w produkcji rur ewoluowały, oferując materiały i rozwiązania dostosowane do szerokiego spektrum zastosowań, od prostych instalacji domowych po skomplikowane systemy przemysłowe. Wśród najpopularniejszych materiałów wykorzystywanych do produkcji rur znajdują się polietylen (PE), polichlorek winylu (PVC) i stal....
Poszczególne etapy planowanej inwestycji najczęściej realizowane są w następującej kolejności:
- lokalizacja inwestycji,
- określenie warunków hydrogeologicznych,
- określenie przekroju,
- wybór materiału geomembranowego,
- określenie jego grubości,
- zaplanowanie detali związanych ze skarpami i obsypką,
- zaplanowali detali związanych z rowem kotwiącym,
- oszacowanie stateczności skarp i warstw obsypki,
- wykonanie projektu i opisanie szczegółów konstrukcyjnych,
- wybór strategii badań spoin (niszczących i nieniszczących),
- projektowanie połączeń i wyposażenia,
- kontrola powstawania nieszczelności warstw i sposoby naprawy,
- kontrola jakości,
- odbiór końcowy budowy.
Przygotowanie podłoża
Podłoże gruntowe pod uszczelnienie z geomembrany do głębokości 15 cm powinno być utworzone z gruntów o średnicy ziaren nieprzekraczających 2,0 mm i w zależności od rodzaju obiektu odpowiadać zapisom Rozporządzenia Ministra Środowiska w sprawie szczegółowych wymagań dotyczących lokalizacji budowy, eksploatacji i zamknięcia, jakim powinny odpowiadać poszczególne typy składowisk [1], oraz Rozporządzenia Ministra Środowiska w sprawie warunków technicznych, jakim powinny odpowiadać budowle hydrotechniczne i ich usytuowanie [2].
Układanie geomembran na podłożu naturalnym wymaga szczególnie dokładnego jego przygotowania, usunięcia korzeni, kamieni i innych ostrokrawędzistych przedmiotów oraz gruntów słabych (torfów i namułów). Nie dopuszcza się układania geomembran na podłożu nawodnionym i przy lokalnych wysiąkach wody. Tego typu powierzchnie powinny być zdrenowane. Ze względu na to, że geomembrany silnie podlegają procesom reologicznym, niedopuszczalne jest pozostawienie kamieni w podłożu. Podłoże powinno spełniać warunki I i II stanu granicznego nośności i użytkowania. Maksymalna dopuszczalna głębokość kolein w trakcie układania geomembrany nie może przekraczać 10 mm. Podłoża betonowe i skalne powinny być starannie wygładzone bez wyraźnych spękań i ostrych krawędzi. Wszelkie załamania powierzchni i naroża powinny być zaokrąglone krzywizną o promieniu ok. 50 mm. Często w takich przypadkach projektuje się zastosowanie geowłóknin ochronnych jedno- lub dwustronnych, co minimalizuje ryzyko przebicia od strony podłoża. W trakcie wykładania geomembran w zbiornikach z płaszczem stalowym należy zwrócić uwagę na dokładność zeszlifowania spoin oraz dokładność usunięcia wszelkich elementów montażowych. Przygotowanie podłoża pod geomembrany powinno być nadzorowane przez geotechnika. Powinna odbyć się wizja lokalna z udziałem przedstawicieli inwestora, wykonawcy robót ziemnych, firmy instalującej geomembranę i nadzoru inwestorskiego. Z wizji lokalnej sporządza się protokół z ewentualnymi zastrzeżeniami co do jakości oraz wszelkimi uwagami dotyczącymi koordynacji prac. |
ABSTRAKT |
W drugiej części artykułu dotyczącego warunków technicznych wykonania i odbioru warstw uszczelnienia z zastosowaniem geomembran omówiono etapy przygotowania podłoża pod uszczelnienie, warunki dostawy i składowania materiału na placu budowy, przebieg kontroli jakości robót i procedury odbioru. Wymieniono metody wykonywania spoin oraz badań nieniszczących i niszczących. |
|
Conduct on construction siteThe second part of the article concerning technical construction and commissioning requirements for layers of sealing the utilise geomembranes discusses subsequent stages of preparing the base for sealing and the conditions for delivery and storage of material on site, as well as the course of work quality control and the commissioning procedure. The article also specifies the methods of performing joints, as well as non-destructive and destructive testing. |
Dostawa geomembran na plac budowy
Do wykonywania uszczelnień z tworzyw sztucznych na różnego rodzaju obiektach dopuszcza się jedynie geomembrany mające deklarację zgodności lub certyfikat zgodności z normą materiałową lub z aprobatą techniczną. Właściwa identyfikacja wyrobu na budowie jest podstawą kontroli jakości wyrobu i decyduje o jakości wykonanego obiektu.
Sam wygląd zewnętrzny geomembrany nie może być podstawą oceny, chyba że wyrób i jego opakowanie są wyposażone w niebudzące wątpliwości znaki identyfikacyjne producenta (FOT. 1-2) i zawierają odpowiednie oznakowania z numeracją partii produkcyjnej i poszczególnych bel wraz z podaniem systemu kontroli jakości producenta.
W przypadku dostarczenia na budowę wyrobu niezawierającego znaków identyfikacyjnych należy przeprowadzić badania polegające głównie na stwierdzeniu, że wyrób posiada parametry zgodne z deklarowanymi w danych producenta i został wyprodukowany z odpowiedniego granulatu (RYS. 1). W przypadku wystąpienia sporu między dostawcą a odbiorcą geomembrany przeprowadza się certyfikację wyrobu.
Certyfikat zgodności jest dokumentem wystawionym przez upoważnioną do tego stronę trzecią, najczęściej akredytowane laboratorium z potwierdzeniem, że dostarczony wyrób na konkretne zadanie jest zgodny z aprobatą techniczną, znakiem CE lub danymi technicznymi wykazanymi w karcie wyrobu.
Każda dostawa na plac budowy powinna posiadać ważne świadectwo systemu kontroli jakości producenta, kartę gwarancyjną producenta materiału oraz charakterystyczną i widoczną metkę na każdej beli. Sprawdzeniu podlega:
- nazwa producenta geomembrany,
- nazwa handlowa geomembrany,
- rodzaj tworzywa sztucznego,
- nazwa i producent granulatu, z którego wytworzono geomembranę,
- numery rolek z danej partii,
- data produkcji,
- okres gwarancji na dostarczona partię materiału,
- grubość geomembrany,
- wymiary i masa rolki.
W momencie dostawy należy zdjąć lub spisać informacje zawarte na belach i zatrzymać do momentu odbioru całości obiektu. Rozwijanie losowo wybranych bel dla oceny ich jakości w warunkach budowy jest bardzo trudne i rzadko tę czynność się przeprowadza.
Stąd najlepiej dokonać tego w trakcie układania pierwszej partii geomembrany. Należy przy tym zwrócić uwagę na ewentualne uszkodzenia powierzchni, zabrudzenia i istnienie obcych ciał po wewnętrznych stronach rozwijanych bel.
Transport i składowanie geomembran
Czynności związane z transportem, przemieszczaniem wewnątrz budowy oraz składowaniem powinny odpowiadać instrukcji producenta, gdyż od tego również zależy spełnienie warunków gwarancji udzielonej przez producenta. Należy używać sprzętu budowlanego, który nie powoduje uszkodzeń mechanicznych materiału.
Do podnoszenia i przemieszczania należy stosować zawiesia z pasm tkaninowych o gwarantowanych wytrzymałościach na zerwanie (z reguły producenci zaopatrują każdą rolkę materiału w dwa zawiesia z taśm PES) (FOT. 3). Można stosować również belki trawersowe (FOT. 4). Nie dopuszcza się natomiast stosowania zawiesi z lin stalowych.
Materiał powinien być składowany na obszarze chronionym, na suchym i płaskim podłożu, oczyszczonym z ostrokrawędzistych ziaren i przedmiotów, a także zabezpieczonym przez wpływami atmosferycznymi (FOT. 5).
Jeżeli instrukcja producenta nie przewiduje inaczej, belki geomembrany należy składować w 3-4 warstwach w formie pryzmy lub z przekładkami międzywarstwowymi w postaci belek drewnianych. Dolna warstwa powinna być zabezpieczona przed stoczeniem się drewnianymi klinami.
Kontrola i zapewnienie jakości na budowie
Ze wszystkich do tej pory znanych geosyntetyków żaden nie jest tak wymagający jak geomembrany. Najmniejsza nieszczelność materiału lub połączenia może spowodować wyciek izolowanej cieczy pod ciśnieniem hydrostatycznym.
Dlatego tak ważne jest opracowanie i wdrożenie kontroli jakości (KJ) i procedur zapewnienia jakości (ZJ). Należy pamiętać, że woda gruntowa lub swobodnie płynąca jest żywiołem nieznoszącym jakichkolwiek błędów ludzkich.
Plan kontroli jakości
Plan kontroli jakości powinien być uzgodniony między projektantem, inspektorem nadzoru i wykonawcą. Prawidłowy tok postępowania prowadzący do zapewnienia jakości uszczelnienia zawiera:
- udokumentowanie rozładunku przywiezionych rolek geomembrany (sprawdzenie i opisanie poszczególnych rolek, sprawdzenie atestów producenta, numeracji rolek itp.);
- kontrolowanie składowania i przenoszenia rolek na budowie;
- wyselekcjonowanie próbek do badań (w przypadku wątpliwości co do jakości dostarczonego materiału);
- sprawdzenie oznaczeń pobranych próbek w powiązaniu z numeracją fabryczną rolek i przy zaznaczeniu kierunków wzdłuż i w poprzek beli;
- przeprowadzenie wspólnego przeglądu wykonanego podłoża pod geomembranę przez inspektora nadzoru, wykonawcę robót ziemnych i instalatora geomembrany;
- w trakcie układania geomembrany - codzienne notowanie w dzienniku budowy warunków pogodowych (temperatury, wilgotności powietrza, opadów deszczu i intensywności wiatru). Jeżeli warunki pogodowe są niezgodne z warunkami określonymi w planie kontroli jakości, inspektor nadzoru zobowiązany jest przerwać układanie geomembrany;
- sprawdzenie poprawności rozmieszczania poszczególnych rolek w powiązaniu z projektem;
- przed rozpoczęciem i zakończeniem wykonywania spoin - wykonanie próbnego zgrzewania. Pobrane próbki ze spoin należy zerwać na zrywarce polowej na budowie. Jeżeli próbnie wykonane spoiny nie odpowiadają jakościowo wymaganiom producenta, należy odrzucić brygadę wykonującą roboty lub sprzęt stosowany na budowie;
- w odniesieniu do kolejno wykonywanych spoin - przyjęcie sposobu oznaczania i udokumentowanie tego na planie montażu (należy wpisać nazwisko operatora sprzętu, rodzaj stosowanego sprzętu, datę i godzinę wykonania konkretnej spoiny oraz warunki pogodowe);
- kontrolowanie na bieżąco każdej spoiny jedną z metod nieniszczących;
- wybranie miejsca pobrania próbek do badań niszczących. Inspektor nadzoru powinien nadzorować wycinanie próbek przez ekipę instalatora geomembrany. Pobieranie próbek powinno być również udokumentowane z określeniem miejsca pobrania, daty, warunków otoczenia, numeracji;
- interpretowanie na bieżąco wyników badań polowych i laboratoryjnych przez inspektora nadzoru i przez instalatora w celu przyjęcia lub odrzucenia wykonanej partii robót;
- ścisły nadzór załatanych miejsc pobrania próbek do badań niszczących oraz przeprowadzenie badań nieniszczących nowo wykonanych spoin;
- w czasie wykonywania robót - systematyczny przegląd całej powierzchni geomembrany służący zlokalizowaniu i udokumentowaniu różnych defektów;
- przed układaniem warstwy ochronnej - odbiór zakrywanej części geomembrany. Układanie obsypki na powierzchni geomembrany powinno być ściśle nadzorowane, gdyż może spowodować jej uszkodzenie.
Układanie geomembrany
Najważniejszym aspektem instalacji geomembran są spoiny - połączenia poszczególnych arkuszy geomembrany. Prawidłowe wykonawstwo spoin decyduje o szczelności całego układu. Dlatego też zagadnienie to powinno być przedmiotem opracowań praktycznych i teoretycznych skierowanych do wszystkich uczestników procesu inwestycyjnego.
Osiągnięcie stosownego zasobu wiedzy na temat połączeń geomembran na budowie nie tylko przez operatora sprzętu zgrzewającego, lecz także przez projektanta i nadzór inwestorski powinno doprowadzić do eliminacji wielu błędów.
Poszczególne bele geomembrany powinny być rozmieszczane na placu budowy tak, aby ograniczyć do niezbędnego minimum ich przemieszczanie (FOT. 6). Rozwijanie poszczególnych bel powinno odbywać się za pośrednictwem specjalnych belek trawersowych, osi z kółkami ogumionymi lub stojaków łożyskowanych.
Należy przestrzegać zasad układania poszczególnych arkuszy geomembrany:
- najpierw instalować pasma na skarpach, rozwijać je od korony do podstawy skarpy, unikając przy tym wszelkich zbędnych naprężeń w geomembranie;
- poszczególne pasma układać prostopadle do skarpy, dzięki czemu spoiny nie stanowią przeszkody dla spływu wód opadowych;
- unikać układania geomembrany na zbyt stromych skarpach. Jest to często przyczyną awarii uszczelnienia;
- w dnie składowiska rozwijać poszczególne pasma wzdłuż spadku dna, zaczynając od najniższego punktu;
- unikać schodzenia się wielu spoin w jednym punkcie, szczególnie w narożach uszczelnianych obiektów.
Zaleca się rozwijanie pasm przewidzianych do zgrzewania w danym dniu o jednakowej porze, aby wyeliminować napięcia wynikające z efektów temperaturowych. Wynikiem korozji naprężeniowej może być rozerwanie materiału w miejscu połączenia. Powierzchnie kontaktu, czyli zakłady poszczególnych pasm, powinny być wyrównane na całej długości i mieć jednakową szerokość dla danej technologii łączenia.
Powierzchnie kontaktowe łączonych pasm powinny być wolne od zanieczyszczeń, kurzu, wilgoci i innych substancji obcych. Optymalna temperatura otoczenia w trakcie wykonywania połączeń powinna wynosić od +5°C do +40°C.
Nie należy dopuszczać do tego, aby roboty były wykonywane w temperaturze geomembrany niższej niż +5°C. Łączenie geomembrany przy niższych temperaturach otoczenia dopuszcza się sporadycznie pod warunkiem stosowania na budowie specjalnych tuneli ocieplanych.
Wykonywanie robót w takich warunkach powinno być poprzedzone odpowiednim przygotowaniem łączonych powierzchni i prowadzone pod szczególnym nadzorem niezależnej jednostki badawczej. Nie należy również prowadzić tego rodzaju robót w trakcie silnego wiatru i deszczu. Wilgoć w istotny sposób wpływa na jakość spoin, dlatego każdorazowo przed rozpoczęciem robót należy sprawdzić punkt rosy.
Metody wykonywania spoin
Podstawowy mechanizm łączenia geomembran polimerowych polega na tymczasowej reorganizacji struktury polimeru przez stopienie lub zmiękczenie na dwóch przyległych powierzchniach, które są poddawane procesowi łączenia w kontrolowany sposób, tak aby po przyłożeniu nacisku oba arkusze zostały trwale połączone.
Ta reorganizacja jest skutkiem dopływu energii wydzielającej się w wyniku zachodzących procesów cieplnych lub chemicznych. Niektóre procesy lub techniki zgrzewania wymagają wprowadzenia innego polimeru w obszar spoiny. Właściwości obszaru wykonanej spoiny są funkcją rodzaju geomembrany i zastosowanej techniki łączenia arkuszy.
Do procesów cieplnych należy:
- spawanie ekstruzyjne:
- spoina pachwinowa (RYS. 3),
- spoina płaska (metoda już niestosowana) (RYS. 4), - zgrzewanie:
- gorącym klinem (RYS. 5),
- gorącym powietrzem (RYS. 6).
Do procesów chemicznych należy:
- fuzja chemiczna (RYS. 7),
- fuzja chemiczna w zagęszczonym rozpuszczalniku (RYS. 8),
- klejenie:
- klejem chemicznych (RYS. 9),
- klejem kontaktowym (RYS. 10).
Poza tym stosuje się jeszcze metodę ultradźwiękowa i elektryczną.
Spoiny spawane ekstruzyjnie
Spoiny spawane (RYS. 11), zwane także spawaniem ekstruzyjnym, w formie spoiny powierzchniowej stosuje się rzadko, jedynie w miejscach trudno dostępnych, do łatania dziur, miejsc po pobranych próbkach do badań niszczących i do wykonywania spawów wokół elementów przenikających geomembranę, tj. wszelkiego rodzaju rurociągów odciekowych, zasilających, studni itp.
Technologia wykonania tego typu spoin (FOT. 7) polega na wykorzystaniu urządzenia zwanego ekstruderem roztapiającego drut wykonany z tego samego materiału co geomembrana. Pasmo roztopionego polimeru nakłada się na krawędź górnego pasma geomembrany.
Górna i dolna płyta są wcześniej podgrzewane miejscowo gorącym powietrzem, a dodatkowa energia cieplna od roztopionego drutu polietylenowego powoduje częściowe roztopienie obu łączonych powierzchni. W wyniku tych operacji roztopione masy się przenikają i tworzą jednolite połączenie.
Proces wstępnego ogrzewania łączonych powierzchni musi być ściśle kontrolowany, aby uniknąć przegrzania osłabiającego strukturę geomembrany w rejonie spoiny. Aby uzyskać połączenie obu płyt, należy stosować docisk łączonych krawędzi.
Szybkość wykonywania spoiny wynosi 30-50 m/h, a stapianie i napawanie odbywa się w temp. 250°C. Prawidłowość połączenia obu pasm w tej technologii wymaga wstępnego oczyszczenia obu płaszczyzn przez zeszlifowanie flexem na szerokości odpowiadającej szerokości wykonanej spoiny.
Zgrzewanie
Istnieją dwie metody zgrzewania (stapiania) geomembran. Są to:
- metoda gorącego powietrza,
- metoda gorącego klina.
Obie wymagają stopienia części przylegających do siebie powierzchni. Ważną rolę odgrywa tu temperatura, nacisk i prędkość zgrzewania. W metodzie zgrzewania gorącym powietrzem wykorzystuje się urządzenie składające się z nagrzewnicy oporowej w formie klina i wewnętrznej dmuchawy oraz regulatorów temperatury (FOT. 8).
Bezpośrednio po stopieniu powierzchni obszar ten jest dociskany celem połączenia obu płaszczyzn. W zależności od kształtu dmuchawy oraz rolek dociskowych otrzymujemy zgrzew jedno- lub dwuśladowy (RYS. 12).
Metoda gorącego klina polega na zastosowaniu elementu oporowego w kształcie klina z wbudowanym systemem grzałek elektrycznych i termostatu przesuwającego się między arkuszami geomembrany. Powierzchnie łączonych arkuszy topią się i przez płynny ruch ślizgowy przesuwają się do rolek dociskowych lub wałków, dzięki czemu otrzymuje się gotowy zgrzew.
Standardowa zgrzewarka wykonuje pojedynczy zgrzew o stałej szerokości, natomiast zgrzewarka z podwójnym klinem wykonuje dwa równoległe zgrzewy z pozostawieniem pośrodku kanału powietrznego o stałej szerokości, który wykorzystuje się do ciśnieniowych badań szczelności. Na RYS. 13–14 przedstawiono schematy różnych połączeń za pomocą gorącego klina.
Sprzęt najnowszej generacji do zgrzewania dwuśladowego (FOT. 9-10) wyposażony jest już w elektroniczny system kontrolny, który umożliwia dzięki rejestracji parametrów łączonej spoiny wskazanie wadliwie wykonanych odcinków. Średnia temperatura klina zależy od warunków otoczenia i grubości materiału i wynosi 300–380°C. Prędkość zgrzewania to 70-90 m/h.
Plany i schematy montażu
Bardzo istotną rolę w kontroli jakości robót uszczelnieniowych odgrywa bieżąca inwentaryzacja układu poszczególnych arkuszy geomembrany. Tego typu plany i schematy montażu powinny być integralną częścią projektu. Wykonawca przed przystąpieniem do robót powinien przedstawić nadzorowi do zatwierdzenia plan z ewentualnymi poprawkami.
Szczegóły konstrukcyjne przejść rurowych, uszczelnień i połączeń z obiektami żelbetowymi lub stalowymi powinny być bezwzględnie opracowane, a ich wykonanie na budowie powinno być prowadzone pod szczególnym nadzorem.
Na planie montażu należy na bieżąco nanosić postępy robót z podaniem numerów bel i numeracją spoin. Wszystkie spoiny powinny być poddane badaniom nieniszczącym, a miejsca poboru próbek do badań niszczących nanoszone z dodatkową numeracją.
Zgodnie z planem montażu powinny być dokonywane wszystkie wpisy do dziennika budowy i do protokołów kontroli jakości wymaganych normą. Po zakończeniu montażu konstrukcji geomembrany plan montażu stanowi podstawę odbioru robót i jest archiwizowany u inwestora.
Kontrola jakości wykonanych zgrzewów
Przed przystąpieniem do robót w danym dniu w obecności przedstawiciela nadzoru należy przeprowadzić próbne zgrzewanie lub spawanie, aby sprawdzić sprawność sprzętu i dobrać odpowiednie parametry urządzeń do warunków atmosferycznych panujących na budowie.
Próbne zgrzewanie przeprowadza się na dwóch wąskich ścinkach geomembrany o dł. 1-3 m, najlepiej, aby była na nich jedna spoina ciągła, co pozwoli spełnić wszystkie wymogi badania.
Badania wytrzymałościowe przeprowadza się na próbkach pasmowych o szerokości 25 mm wyciętych z odcinka poddanego próbnemu zgrzewaniu. Podczas wykonywania tego typu badania wstępnego można ograniczyć do minimum konieczność pobierania próbek do badań niszczących na budowie. Można wykorzystać do tego zrywarki ręczne oraz mechaniczne z rejestracją parametrów (FOT. 11-12).
Dopiero po wykonaniu badań wstępnych można przystąpić do właściwego wykonawstwa zgrzewania geomembrany. Każda spoina powinna zostać skontrolowana na bieżąco za pomocą jednej z metod nieniszczących, na całej długości i w obecności nadzoru inwestorskiego.
Wyniki badania należy wpisać do protokołów (w przypadku metody ultradźwiękowej należy prowadzić dokumentację według zaleceń producenta urządzenia pomiarowego). Do zalecanych nieniszczących metod badania wykonanych spoin należą:
- metoda ciśnieniowa,
- metoda próżniowa,
- metoda ultradźwiękowa,
- metoda piezoelektryczna.
W przypadku sensorowej metody ciągłej kontroli szczelności konstrukcji geomembrany można zrezygnować z nieniszczących metod kontroli szczelności spoin. Zastosowanie metody sensorowej nie zwalnia jednak z konieczności przeprowadzenia niszczących badań wytrzymałościowych spoin.
Jeżeli stwierdzono uszkodzenie spoiny, należy je zlokalizować, naprawić i sprawdzić nowe spoiny metodą próżniową. Jakiekolwiek naprawy geomembrany należy wykonywać na bieżąco, za pomocą tego samego materiału i tej samej technologii wykonywania spoin.
Na każdej budowie należy pobrać próbki do badań niszczących i przesłać je do niezależnego laboratorium celem uzyskania oceny wytrzymałości wykonanych spoin. Z badań niszczących należy sporządzić protokół. Próbki należy pobierać po każdych 250 m wykonanych spoin. Liczba pobranych próbek nie powinna być jednak mniejsza niż trzy dla danego obiektu.
Inspektor nadzoru powinien ściśle nadzorować załatanie otworów powstałych po pobraniu próbek i zbadanie jakości nowych spoin jedną z metod nieniszczących. Wyniki badań nieniszczących i niszczących wykonanych spoin powinny stanowić podstawę do odbioru wykonanego uszczelnienia.
Metoda ciśnieniowa
Metodę tę stosuje się do kontroli spoin dwuśladowych o dł. do 50 m (FOT. 13-14). W przypadku spoin dłuższych należy podzielić je na krótsze odcinki. Badanie to polega na wywarciu ciśnienia wewnątrz kanału powietrznego 200 kPa. Jeżeli w ciągu 5 min ciśnienie nie spadnie więcej niż 10%, spoinę uznaje się za szczelną.
Metoda próżniowa
Na wybrane losowo miejsca wzdłuż spoiny spawanej nakłada się przezroczysty klosz próżniowy i wytwarza podciśnienie 3-4 kPa. Jeżeli w określonym czasie nie pojawią się pęcherzyki powietrza na powierzchni zwilżonej roztworem mydlanym, spoinę można uznać za szczelną. Na FOT. 15 pokazano aparaturę do badań próżniowych.
Metoda ultradźwiękowa
Spoinę można uznać za szczelną, jeżeli daje się penetrować bez przeszkód i bez występowania echa pośredniego na dystansie odpowiadającym trzem grubościom geomembrany lub 10 mm. W ten sposób otrzymuje się potwierdzenie jednorodności wykonanego połączenia.
Metoda piezoelektryczna
W tej metodzie wykorzystuje się ręczne urządzenia w kształcie pistoletu elektrycznego (FOT. 16). Na końcówce mosiężnej uzyskuje się prąd o napięciu 10-50 kV.
Jeżeli w spoinie znajduje się jakakolwiek przerwa (nawet mikronowa), wytwarza się charakterystyczny, niebieski łuk elektryczny przepływający przez ten punkt do podłoża.
Najnowszą odmianą tej techniki jest wtopienie w spoinę bezpośrednio przed spawaniem ekstruderem cienkiego drutu miedzianego lub ze stali nierdzewnej, który podłącza się do napięcia 20 kV (ale o małym natężeniu). Jakakolwiek nieszczelność spoiny wywołuje alarm w przesuwanym nad spoiną detektorze.
Metody niszczące
W tej metodzie wykorzystuje się zrywarki ręczne lub automatyczne z dodatkowym rejestratorem parametrów zrywania. Kryterium jest pomiar wartości niszczącej siły dopuszczalnej i kształt spoiny w momencie zerwania:
- w badaniu na ścinanie spoina powinna wykazać 90% wytrzymałości geomembrany na rozciąganie przy płynięciu,
- w badaniu na odrywanie spoina powinna wykazać 70% wytrzymałości geomembrany przy płynięciu.
Na RYS. 15-16 pokazano schematy badań połączeń geomembran na ścinanie i rozrywanie.
Odbiór robót uszczelnieniowych
Odbiór wykonanej geomembrany powinien odbywać się w obecności przedstawicieli inwestora, wykonawcy geomembrany, nadzoru inwestorskiego, państwowego inspektora sanitarnego, inspektora ochrony środowiska i firmy wykonującej warstwę drenażowo-ochronną. Należy dokonać szczegółowego przeglądu całej wykonanej geomembrany, ze szczególnym zwróceniem uwagi na miejsca połączeń z elementami konstrukcyjnymi składowiska.
Podstawą odbioru geomembrany powinny być:
- projekt uszczelnienia,
- plan montażu geomembrany,
- wyniki badań nieniszczących spoin,
- wyniki badań niszczących spoin,
- protokoły odbioru elementów uszczelnienia,
- dziennik budowy.
Zalecenia końcowe
Przy wykonywaniu uszczelnień z geomembrany należy przestrzegać przepisów BHP i przeciwpożarowych. Materiały, z których wykonana jest geomembrana, są łatwopalne i w trakcie palenia wydzielają się substancje toksyczne.
Podczas wykonywania robót uszczelniających w pomieszczeniach zamkniętych (zbiornikach) należy zachować szczególną ostrożność w trakcie wykonywania spoin ze względu na możliwość ulatniania się substancji szkodliwych dla zdrowia. Szczególną uwagę należy zwrócić na zagrożenia w trakcie klejenia geomembrany do betonowego podłoża w pomieszczeniach zamkniętych.
Inwestor powinien otrzymać od projektanta geomembrany instrukcję eksploatacji uszczelnienia z geomembrany z zaznaczeniem:
- niedopuszczalnych działań na obiekcie,
- częstotliwości i dokumentowania przeglądów,
- zasad kontrolowania urządzeń obserwacyjnych,
- bezpieczeństwa pracy na obiekcie,
- kontroli przywożonych odpadów.
W instrukcji eksploatacji powinien zostać zawarty sposób postępowania w przypadku stwierdzenia uszkodzeń systemu uszczelniającego.
LITERATURA
1. Rozporządzenie Ministra Środowiska z dnia 24 marca 2003 r. w sprawie szczegółowych wymagań dotyczących lokalizacji, budowy, eksploatacji i zamknięcia, jakim powinny odpowiadać poszczególne typy składowisk odpadów (DzU 2003 nr 61 poz. 549).
2. Rozporządzenie Ministra Środowiska z dnia 20 kwietnia 2007 r. w sprawie warunków technicznych, jakim powinny odpowiadać budowle hydrotechniczne i ich usytuowanie (DzU 2007 nr 86 poz. 579).
3. N. Ivy, "HDPE geomembrane after 20 years of service", "GFR", June/July 2002, s. 18–20.
4. P. Michel, J. Natrop, "Trwałość użytkowania przy zgrzewaniu gorącym gazem", Konferencja "Budowa bezpiecznych składowisk odpadów", Gdańsk 1993.
5. J. Młynarek i in., "Kontrola jakości złączy geomembran. Badania terenowe i laboratoryjne", Seminarium „Geotechniczne aspekty składowania odpadów", Gdańsk 1994.
6. PN-EN 13257:2002, "Geotekstylia i wyroby pokrewne. Właściwości wymagane przy stosowaniu w budowie składowisk odpadów stałych".
7. PN-B-10290:1997, "Geomembrany. Ogólne wymagania dotyczące wykonawstwa geomembran na budowie składowisk odpadów stałych".